STARLITE CREATORS Vol.5Towards a future that people and robots work together!
A close look at the development
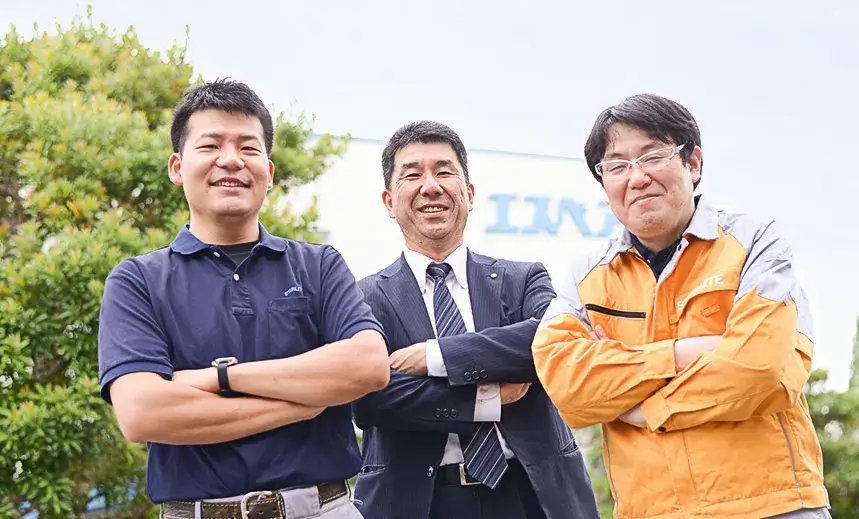
Hi! This is Tsujimoto from Public Relations. Starlite’s original material, S-Bear, revolutionised the Office Automation industry 38 years ago and S-Bear is still at the forefront of the industry. Starlite is trying to take S-Bear to the next level. Doesn’t it sound really exciting!?!?! I decided to interview HT, known as Mr. S-Bear, KT and HH who continue to evolve the product.
Can you please tell me what S-Bear is?
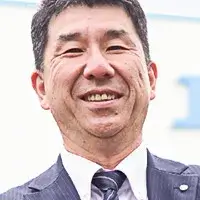
HT:S-Bear is a high-performance plastic material for injection moulding developed by Starlite. Tribology (friction, wear and lubrication) characteristics, heat-resistance, conductivity and flame retardance make it suitable for a wide range of complex applications, used mainly in sliding and drive-train components for office equipment and automotive applications.
How did you start S-Bear development?
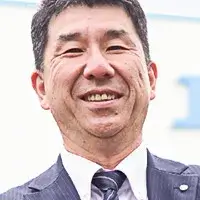
HT:From the late 1970s, office automation equipment such as photocopiers increased rapidly to make office work more efficient. The heart of photocopiers which determine the picture quality reaches above 200 degrees Celsius and the parts that make up this area therefore must be extremely precise and have oil-free drive performance. Due to the large number of parts, injection moulding was the preferred method for mass production, however, it was difficult to achieve required performance with the existing material. This was the starting point for our new material development journey.
In the development of materials at the time, lead was used as a “slip-enhancing technology,” and asbestos was used in brake materials. Nevertheless, the concept for the development of the material was “consideration for the environment and human health”. It was around the late 1980s.
I am very impressed we have been developing sustainable materials from such a long time ago!
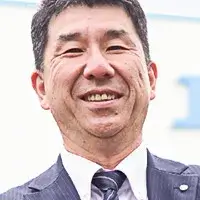
HT:We didn’t call it “sustainable” back then :)
It was not easy to develop materials. To be honest with you, the addition of lead was too effective for heat-resistance, sliding and durability. It was very difficult to find comparable materials. But even so, we took photocopiers apart to investigate the performance requirements of components and kept bothering the customer with our findings. What we had in common was “Let’s make a good product!” and we worked together both internally and externally.
What we have learnt through this activity was to clarify the performance target from the user’s viewpoint and develop a simple material by eliminating unfruitful and excessive functions. We managed to formulate a material that is best effective in niche applications and we collectively call this injection moulding grade as “S-Bear”.
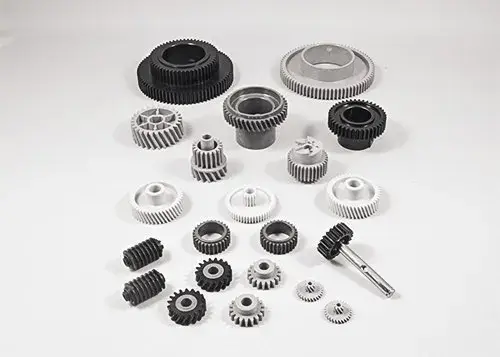
That's amazing!You created the foundation for S-Bear!
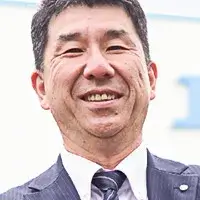
HT:Yes, I feel embarrassed though :)
For example, I developed a gear material called S-Bear S2110 25 years ago, but no other company has yet come up with a material that exceeds its performance. I think Starlite’s material development technology is world class.
Furthermore, designers and developers at Office Automation manufacturers often said “as long as we use S-Bear, we will not have any problems.” This is the best compliment I can get as a birth parent (engineer). I want to bring my children to the forefront of many industries! We are now trying to introduce S-Bear into other industries.
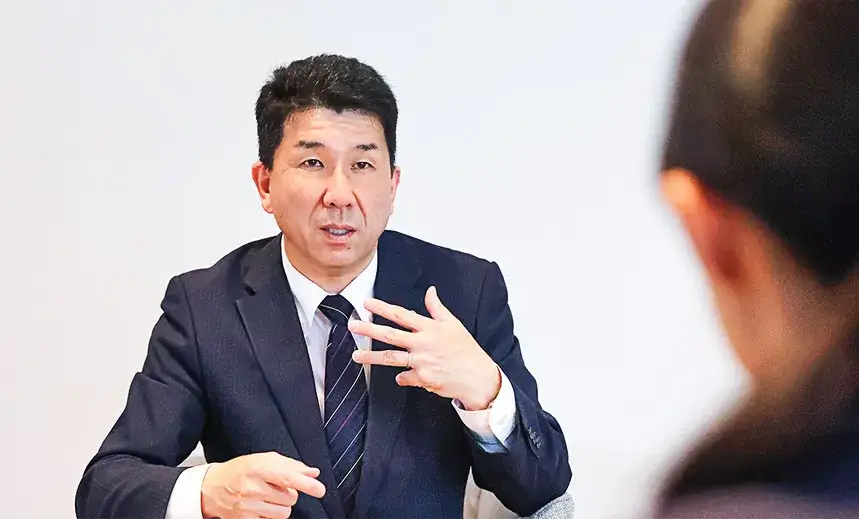
S-Bear is improving… Very exciting!
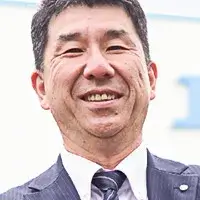
HT:The key is to develop the “next generation S-Bear that matches market needs”. This is what younger generations are working on.
Beyond the mountain of development, there is the “trust of our customers”. Customer voice became my pleasure, pride and confidence. I would like my subordinates to enjoy this precious experience too.
This is a fervent message from your predecessor!
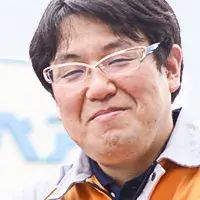
KT:I cannot lose this challenge. At first, I was under a lot of pressure because I felt “I need to develop the next generation S-Bear!” but I started to enjoy my job when I started to think about “For whom and for what”. Nowadays, I have more of a creative desire to complete the project than a sense of mission.
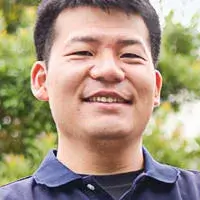
HH:I feel it is Starlite’s tradition to have through discussion with customers. I want to identify problems in the world and solve them instantly with unique and niche materials instead of providing a universal material that pleases everyone. This thought motivates me.
What is the problems that you both want to solve?
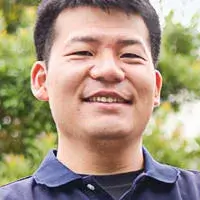
HH:In manufacturing, we have a serious “resource shortage” issue. The shortage of labour has a great impact on productivity and quality for manufacturers like us. In order to solve the problem, the utilisation of small-sized and reasonable “collaborative robots” is increasing.
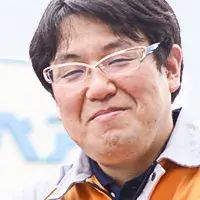
KT:There are robots at manufacturing sites and production efficiency is improving. However, when we have unexpected absence, the rest of the team will suffer and have to work harder because customers’ delivery plan is set so tightly.
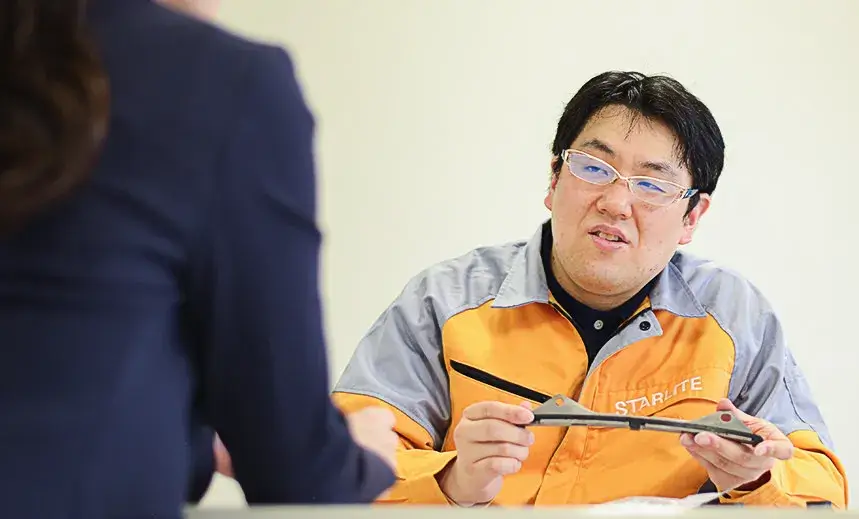
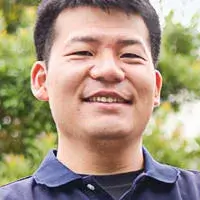
HH:That is when “collaborative robots” become useful. Industrial robots are often large and limited in their installations. However, collaborative robots are small enough to work alongside the operator. For example, a collaborative robot can be placed between two operators on an assembly line. With the right arrangement, a reasonable production line with only robots is not a dream.
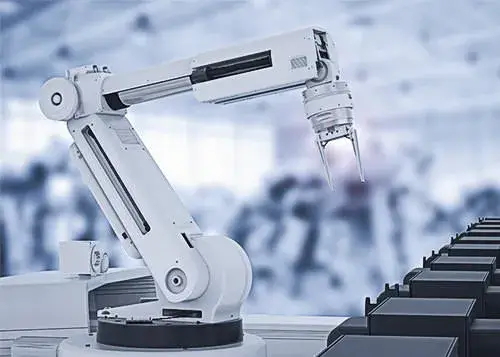
Robots can keep manufacturing, cannot they?
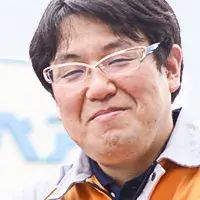
KT:Yes, exactly, but robots have to be highly durable and compact that can be installed anywhere.
What I am developing now is S-Bear gear material that exceeds the characteristics of metal gears for drive applications. I believe that the weight reduction resulting from the metal substitution will make it possible to reduce the size of the motor that drives the arm as well as to reduce noise and make it oil-free.
In particular, the improvement of robot’s mechanical noise can contribute to maintaining the concentration level and reducing mental strain of operators working at close range. Furthermore, Starlite’s deceleration system “Differential Drive,” which consists of S-Bear gears and used for electronic locking units for doors, can make a significant contribution to reducing the size and weight of robot joints.
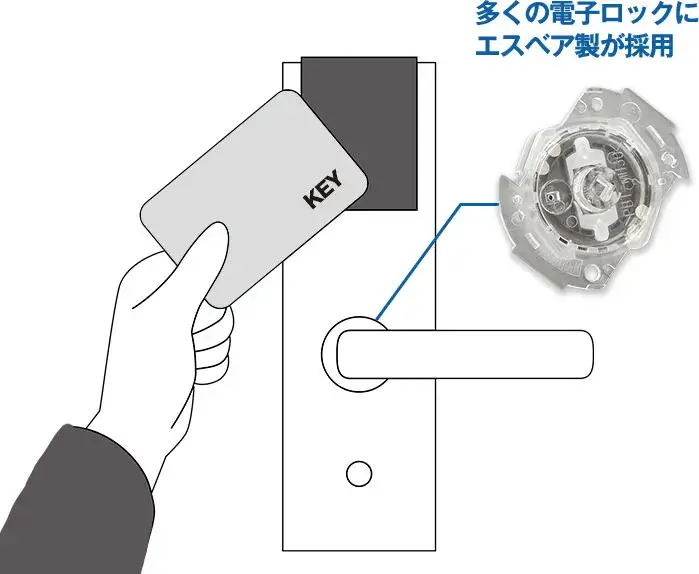
for electronic locks
with different bearing material
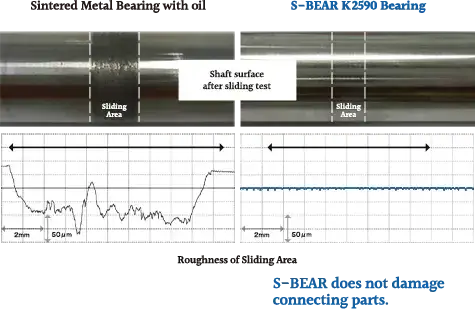
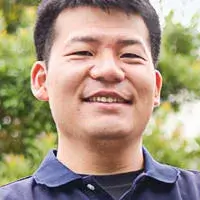
HH:In addition, it is highly important to control collaborative robots accurately in order to improve productivity. The more the arm is moved at high speed, the more it becomes difficult to stop it. Like cars, brake performances are directly linked with drivability and operators’ safety. I developed the brake material which is the heart of the system. The material is effective in reducing the number of parts and weight, which also contributes to downsizing of robots.
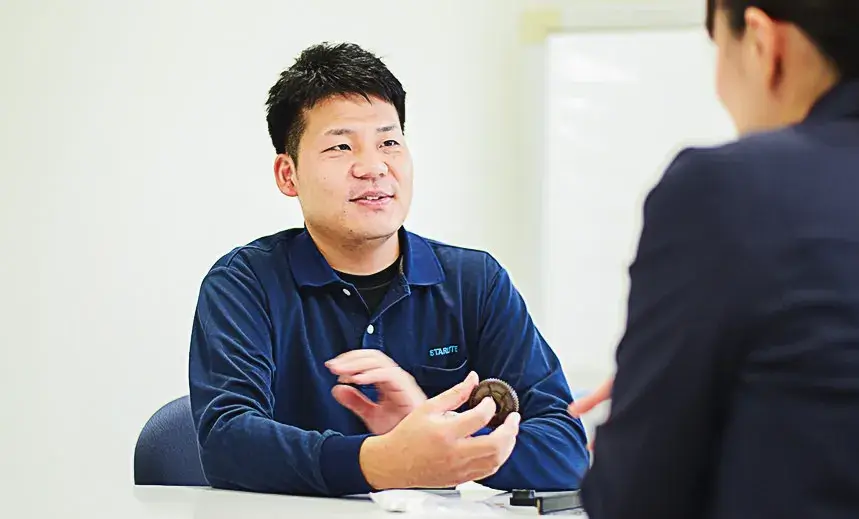
S-Bear is keeping up with the “current trends”!
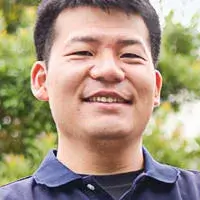
HH:S-Bear has contributed to the spread of Office Automation equipment, and from now on, we will continue to contribute with collaborative robots that will facilitate digital transformation and a new way of working. In doing so, I will have to be very conscious of sustainability as well as making better products.
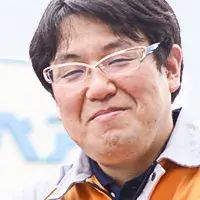
KT:HT mentioned the concept of S-Bear development was “consideration for the environment and human health”. The concept is still the same and it is an unchangeable theme for S-Bear and for Starlite. One of our attempts is “S-Bear development by biomass plastics”. In addition to this, we will try to make more proposals for realising a sustainable society using S-Bear. The most important thing to remember when developing S-Bear is to make sure that the “performance goals are clear from the users’ viewpoints”.
Interview Summary
I, Tsujimoto, was surprised to learn we have been developing materials with sustainability in mind for 25 years! The lyrics of Starlite’s company song include a line “what can we leave behind for our planet.” This represents Starlite’s passion to care for our planet. I am so proud of the engineers who are making this happen.
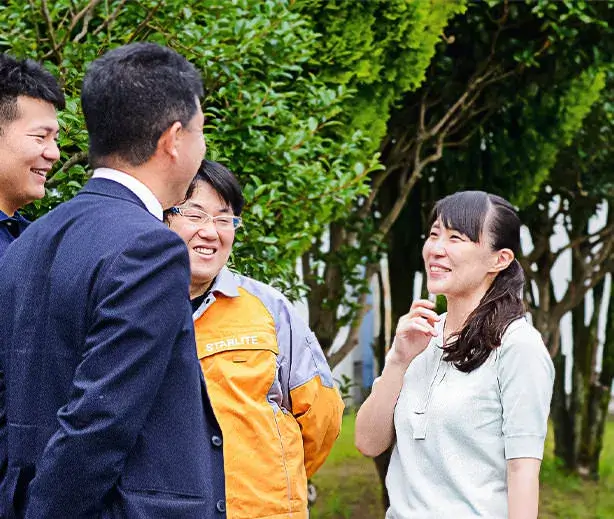
We look forward to working in partnership with you to create new solutions.
The motion engineering material “S-Bear” realises lightweight and compact power transmission parts. It contributes to the high performance of robots, mobility and production machines. Please feel free to contact us.