STARLITE CREATORS Vol.11No defective products for three years! Creators who support the automotive industry, and the future built by a state-of-the-art plant
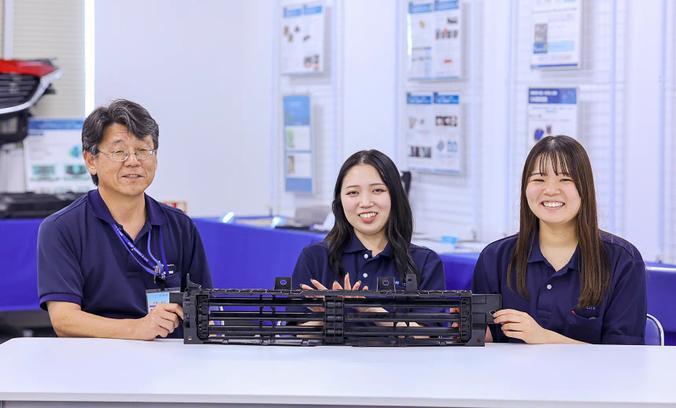
Good afternoon, I am Hanaoka from Public Relations. I am saying this out loud that Starlite makes important parts for automobiles. Today we have creators who have overcome many challenges and continue to improve vehicle performance. We will be presenting their passion for "car making" as a special feature in a total of four issues.
In this first article, I visited the Yamaguchi Plant where Active Grille Shutters (AGS), unit products that contribute to improving performance of automobiles, are manufactured. I interviewed the creators who established the Yamaguchi Plant and the next generation of creators.
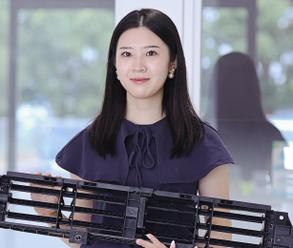
Y.KOne of the people involved in establishing the Yamaguchi Plant. He is absolutely in pursuit of what the Yamaguchi Plant wants to be.
Y.MShe is responsible for arranging the purchase of secondary materials. She supports the production floor. This is her fourth year working after graduation.
U.MThis is her third year and she brightens up the workplace by just being there. She is responsible for production planning.
The Yamaguchi Plant is a new plant established in 2018, right?

Y.K:Yes, this state-of-the-art plant was established based on a group company that had been manufacturing products mainly for automobiles for about 25 years.
Can you explain what the AGS manufactured here is?

Y.K:The AGS is the product used in automobiles that Roechling Automotive, our business partner located in Germany, and Starlite are providing worldwide. The AGS is mounted behind the radiator grille, controls the inflow of outside air into the engine compartment, and reduces energy loss during ambient temperature warm-up... Well, to put it in simple terms, it is a popular unit because the AGS controls air flow, reduces air resistance, and even improves fuel efficiency.
AGS
I hear we have an amazing injection molding machine at the Yamaguchi Plant to manufacture the AGS.

Y.K:Yes, that would be the 1,850-ton double injection molding machine, which is one of the largest in Japan.
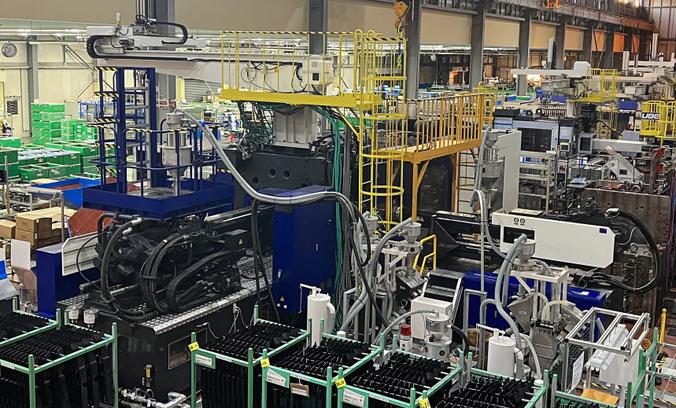
One of Japan's largest! Why do we need the double injection molding machine?

Y.K:The structure of the AGS has two main parts. The air guide that directs air from the bumper opening to the shutter, and the shutter that controls the air coming in and out. A motor moves the shutter flap, so its frame is made of hard materials to prevent the frame from distorting.
On the other hand, the air guide is made of soft materials to adhere closely to the back side of the bumper opening. The large, rigid shutter and the soft air guide frame can be molded together without joints using the double injection molding machine, preventing air from leaking.
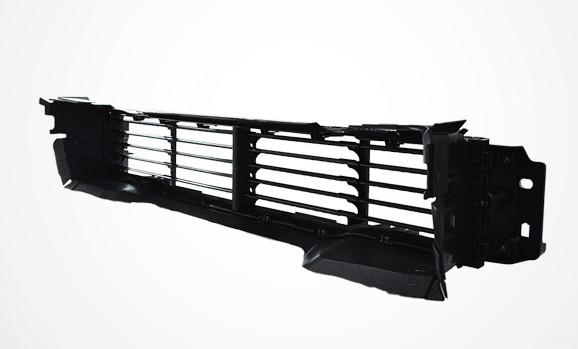
Molding two types of materials at once saves time and improves performance!

Y.K:Yes, that is right. It is much more efficient and effective than making two parts separately and then putting them together later. In the three years since mass production for AGS began, there has not been a single defective product on the market. I think we might be the only company in Japan that can stably manufacture large molded products with such complex structures in multi-cavity mold.
No defective products! So this is the state-of-the-art plant that supports stable production. The Yamaguchi Plant is amazing!

Y.K:But there are more. We have injection molding technology that improves appearance defects, use the in-line production method, and also incorporate collaborative robots for automation.
There are a lot of interesting words that keep coming up. But first things first, what is injection molding technology that reduces appearance defects?

Y.K:First loosely fasten the mold. Then, gradually fasten the mold at high pressure to prevent it from opening, as resin is poured into the mold. If the gas generated while resin melts remains in the mold, they can cause a poor appearance on the product surface. This is the injection molding technology that creates a slight gap to allow gas to escape, but does not generate burrs from the resin that subsequently flows in. In addition to controlling the injection molding machine, there is also expertise required for the mold. If resin burrs remain in the mold, continuous molding may be halted. Click here for the article about moldmaking technology.
Mold Technology That Prevents Appearance Defects
It is very important to take steps to prevent appearance defects of interior and exterior automotive components that are fully visible to users.

Y.K:The Yamaguchi Plant is also promoting manufacturing with an emphasis on efficiency. For example, in-line production method.
That sounds interesting. Please tell me more!

Y.K:The molding area and assembly area are connected on one floor, and the flow of production from the injection molding machine is in a single line. We also do simultaneous production, and the assembly process can complete next to the molding machine.
It is very efficient because you do not have to move the parts!

Y.K:We also have been incorporating the collaborative robots that assist operators. It is designed for consistent assembly even if beginners or trainees join the lines. Since we let the robots take care of simple tasks, we are able to ensure manufacturing with a small number of people and use people's time for new proposals and testing. Mounting small parts into large molded products is physically demanding and makes it difficult to keep quality stable. Therefore, we let the collaborative robots handle that part.
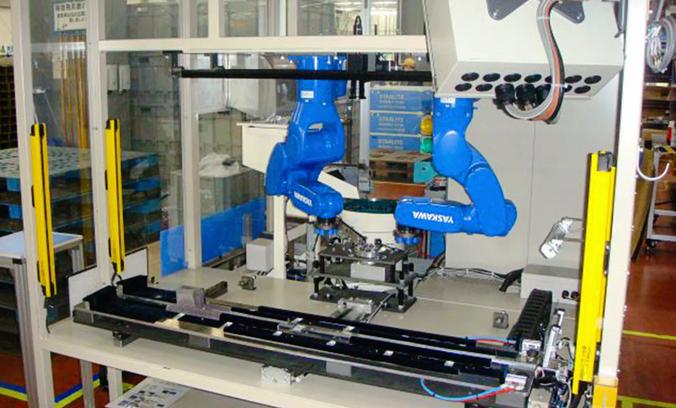
The robots seem like excellent assistants who move quickly and never get tired.

Y.K:An AGF (Automated Guided Forklift) brings finished products assembled by people and collaborative robots to the shipping area. What we are trying now is to have a collaborative robot pick up the injection molded products directly from the automatic extractor. If the grabbing position shifts even slightly, the product will be dropped. But if this works, we are very close to full automation.
We also started using an AGV (Automatic Guided Vehicle) that moves the wagon to transport containers for large products as wide as the width of a car called cowl grille. We are trying to move raw materials in paper bags from the raw material storage area to the molding machine area by AGV too. In addition, we try to let a well-known serving robot seen in some family-style restaurants move secondary materials to the assembly and processing line (working table).
Flow from production to shipment

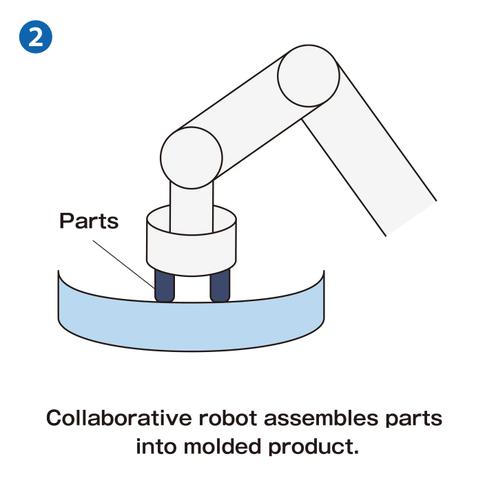
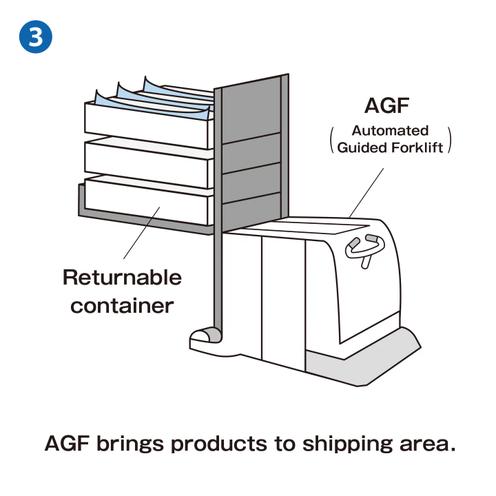
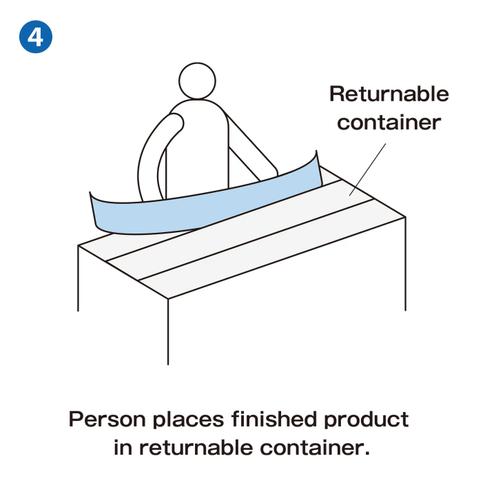
Swipe sideways for more.
You have a lot of ideas for improving efficiency. Where do they come from?

Y.K:I would like to engage in high value-added work while taking advantage of the abilities people possess, and to go forward toward a "manufacturing plant with attractive, state-of-the-art technology" which is the concept behind the establishment of the Yamaguchi Plant. Simply adding more people to night shifts due to shortage in labor will only increase fixed costs and worsen profitability. It is getting more difficult to recruit people now, which is another reason why we want to avoid increase in fixed costs.
We would like to advance our plant with the wisdom of people for better manufacturing.

The Yamaguchi Plant is really moving forward toward the "attractive manufacturing plant". It is very important to be sensitive enough to notice "waste" and "inefficiency".

Y.K:We have started DX initiatives not only on the production floor, but also in the production management, the heart of the plant. For example, in the shipment verification, scanning the bar-code on a product automatically checks the required checklist. It would be nice if we can install monitors near each molding machine to show the status of all molding machines in the plant as well as the operational status or any issues at a glance.

U.M:That would be great.

Y.K:The progress can also be viewed through a tablet, which will allow us to see any updates anywhere.

U.M:That is nice. We do not have to walk around the plant then.

Y.K:If we scan a bar-code to confirm the completion of assembly and the status is shared on the monitors, all progress will be visible anywhere in the plant to make sure that there are no delays.

U.M:Yes, that sounds good too. I usually go to the production floor every one or two hours, but I will be able to see all the production progress even from my desk in the office. That would make our job a lot easier, and we can focus on our daily work at our desk.

Y.K:But it is not good to just sit at your desk all day. Because if you go and look around the production floor, you often notice things that need improvement.
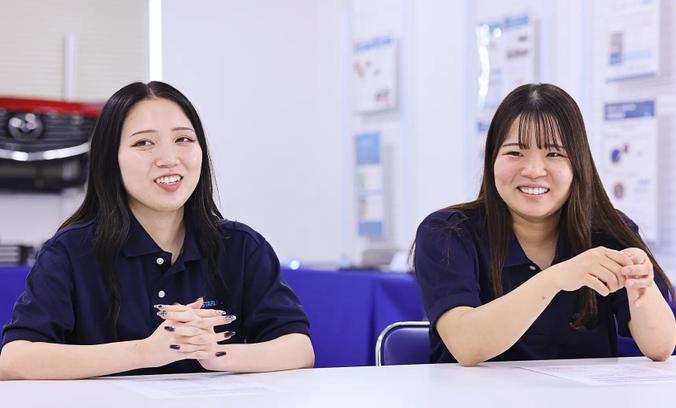
The Yamaguchi Plant still has plenty of space on the site, right?

Y.K:Yes, we also plan to build a second plant. We have already made concept drawings and researched construction and estimated costs so that we can start anytime. We would like to incorporate water circulation systems.
What are the "water circulation systems"?

Y.K:Whenever we switch injection molds, we have to remove all the coolant that has accumulated in the mold, which amounts to about 40 to 60 liters per side of the mold. We would like to create a system where water can be collected and reused, rather than being used once and then drained.

U.M:Yes, I agree. It is of course better not to dispose of the water after a single use. We should be able to come up with more ideas for the second plant!
You two will be leading the Yamaguchi Plant. I would like to ask you both about your dreams and what you would like to do in the future!

Y.M:It would be nice to have a system that allows us to instantly talk to people in different locations at the push of a button. When the second plant is built, going back and forth between the plants will cause time loss, so it will be very convenient to be able to see each other and communicate with each other anytime, anywhere. When you want to ask for something or have a message, it is better to be able to see facial expressions and gestures so that the message can be conveyed clearly and tasks can be performed more quickly too. It would be interesting to have a system where we can talk face to face not only with people at the Yamaguchi Plant, but also with people at other locations, or even with people overseas.

Y.K:Yes. It may be nice if we could talk to people at each location on the screen right away when we talk to the large monitor. I will feel comfortable if I know exactly who I am talking to, and I am sure we will be able to exchange more information and increase communication that way.
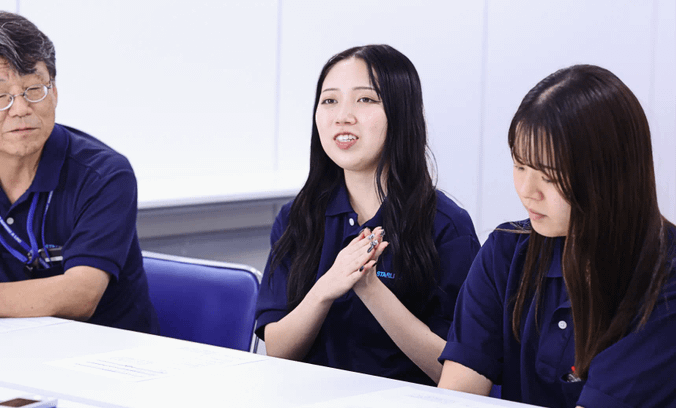
It would be nice to make good use of digital technology to make work more efficient, make communication more active, and create a place where more ideas are born.

U.M:I think it would be interesting if we could manufacture our own brand car from scratch at the Yamaguchi Plant. It seems that vehicles at speeds of 19 km/h or less can be built relatively freely, and it would be convenient and fun to use it as a mobility vehicle that can travel between the first and second plants.
It is very possible since we are working on a prototype of an ultra-lightweight next-generation mobility carrier.

U.M:It would be entertaining to make the brand car in the shape of an anime or manga character. I would like to see and ride in such a car, because I love the manga character "Opanchu Usagi". It would be fun to see a variety of characters or to be able to redecorate the inside of the car with a different character.
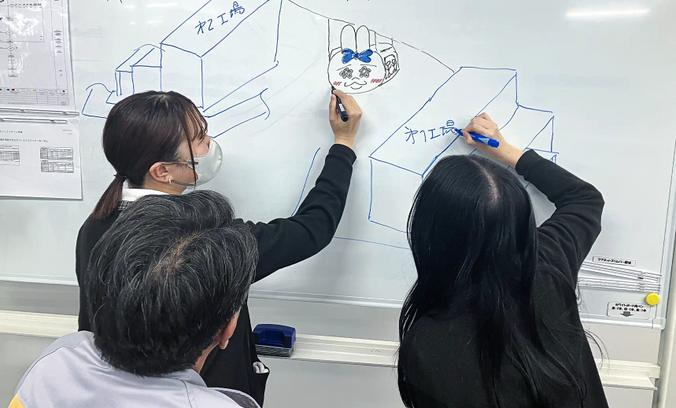
Wow, that can cheer us up and it will be a nice change of pace!

Y.M:We will be even more motivated if we can customize our uniforms. If I could choose a design while using the same logo, it would lift my spirits because I get to wear the uniform of my choice. I like wearing black or a little bit tight. And we will wear something more formal when meeting with customers.

U.M:If we can incorporate a bit of playfulness into our daily work, we may find easier to propose free ideas. We would like to create an environment that encourages people to come up with a lot more interesting ideas.
A lot of things to do! It looks like the Yamaguchi Plant will evolve further as a place overflowing with ideas!

Y.K:My dream is that someday people would say that the Yamaguchi Plant is the mother plant of Starlite Group as a manufacturing plant with attractive, state-of-the-art technology that proposes new ways of working, in addition to manufacturing.
It is a huge evolution if the Yamaguchi Plant exceeds the Ritto Plant, the current mother plant!

Y.K:Yes, we would like to manufacture products using super engineering plastics, which have already been done at the Ritto Plant. Super engineering plastics are the materials with excellent heat resistance and strength, but they are very difficult to mold. However, we should take on challenges, and become the plant that exceeds the Ritto Plant.

U.M:We should steal new businesses from them! We would like to continue providing the world with products that will make everyone happy!
Interview summary
It was exciting to hear so many new ideas for the second plant that is slated to be built at the Yamaguchi Plant, which began operations in 2018. It was as if a grownup in the neighborhood and children filled with dreams enjoyed chatting with each other, and I felt happy just watching them. It is nice just to be able to freely express their thoughts and ideas, as the interview went smoothly with a warm relaxed tone from start to finish. I look forward to the future of the Yamaguchi Plant that will continue to evolve and become a state-of-the-art, attractive manufacturing plant.
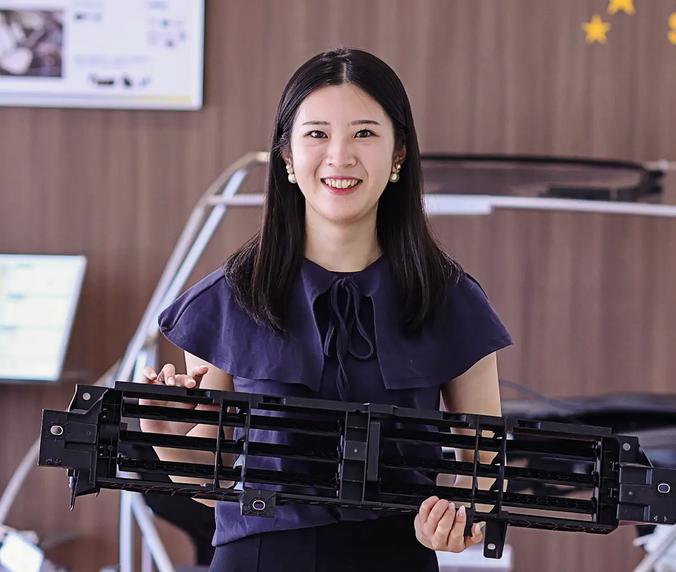
We look forward to working in partnership with you to create new solutions.
Starlite develops and manufactures functional products for automobiles, such as AGS and cowl grilles. We contribute to solving various issues such as reducing vehicle weight, protecting pedestrians from collision, and improving fuel efficiency. Please contact us at anytime.