STARLITE CREATORS Vol.8What is common knowledge of “the team that is determined to succeed?” - Development of Super Heat-Resistant Material – Next Generation BAKES
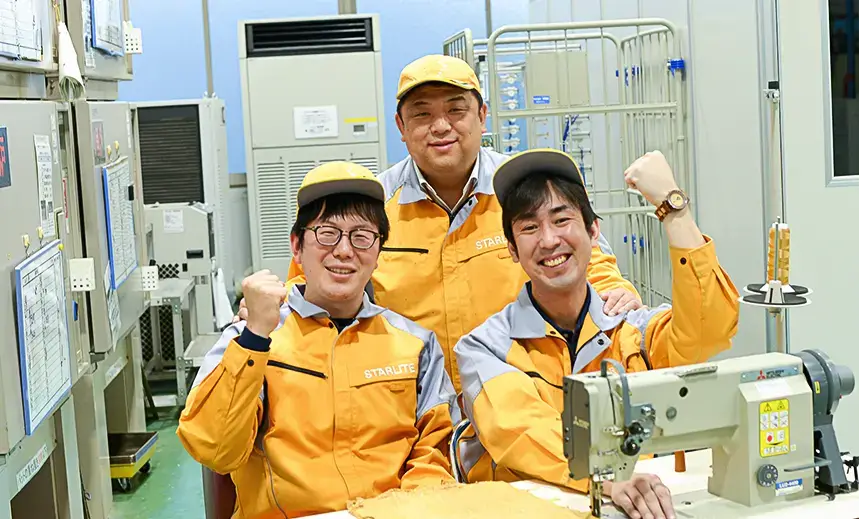
Hi! This is Tsujimoto from Public Relations. Today, I am at the site where the team is developing “the next generation BAKES,” a super heat-resistant material, that is hoped to be used in semiconductors and aerospace applications. Oops! I am stared at! Three of them are looking at me with huge smiles. Let’s talk to them!
Thank you very much for allocating time fo ………..

SW:I’ve been waiting for you! Can I start to talk now?
Hi, This is S. We are not improving the existing BAKES in this team. We are developing a completely NEW BAKES. This is something we have not been able to achieve, but we will do whatever it takes to make it happen! In doing so, we are not afraid to deny our achievements and ignore our traditions. This is what people call us…

WY:Stop, stop! Tsujimoto san is stepping back 50 centimetres. Sorry about that, let me explain again.
There is an image that plastic is weak against heat, however, it is not so true. BAKES, a heat-resistant resin material, developed by Starlite about 80 years ago, is based on a thermosetting phenolic resin and it is used in severe conditions such as steelmaking processes where red-hot iron flows. One of our team’s missions is to develop super heat-resistant BAKES for ceramics and glass making processes where temperatures are higher than steelmaking.

SW:Our team slogan is “Destruction and Creation.” We are developing a material outside of the box of conventional phenolic resin. To be specific, phenol is good because of its hardness and excellent impregnability* for heat-resistant and highly durable applications. Leader I threatened, oops, advised us, saying “Break the existing concept and think hard!”
- Impregnability: Property of a synthetic resin to penetrate into gaps in a tissue or structure of a fabric.
BAKES has 80 years of technology behind it! How dare you destroy that… (oh no!)

SW:We are aiming to develop materials that demonstrate excellent sliding performance under conditions that are 200 degrees higher than the heat resistant characteristics of BAKES. We gave up on phenolic resin, which is the “ordinary” material for BAKES, and switched to polyimide resin! The development of materials based on the phenolic resin is easier because we have a lot of proven data and mass production experiences. However, when we require absolute heat-resistance, I decided to choose polyimide resin which has not been studied much at Starlite. There are many complexities with polyimide resin, but one of them is that it does not penetrate into reinforced materials like phenolic resin, which means that we need to find a new dispersion method and molding process. In addition, polyimide resins are very expensive, so we have to find applications that match the value of the material.
Whilst I, with a one-track mind, was searching through literature and past data to come up with material composition, Leader I was already thinking about processing and mass-production methods before anyone knew. WY was visiting customers’ sites to find a place where super heat-resistant BAKES could be applied. Everyone is very nosy :) That is why I keep thinking of more and more material ideas. There are many people who foment the idea of the trend word, innovation, but when I ask, “so where do you start from?,” most of them are not able to give me concrete ideas. However, even though we are told we are old-fashioned, we are eager to tackle problems, do what we are good at, and do whatever it takes to get the results we want!
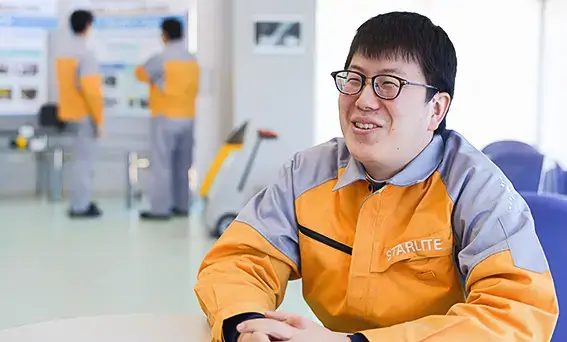

SW:Now, moving on to WY’s story! He is not even using resin as a development material! :) “THE DESTRUCTION AND CREATION!”
What? You are not using resin…? Isn’t it a problem?

WY:Yes, no resin. Most of BAKES products are molded in resin, however, “BAKES-TT” that I developed is a heat-resistant fabric, a mat. It is used on the aluminium extrusion processes, withstands high temperatures of up to 500 degrees without damaging the extruded aluminium products and has a long service life.
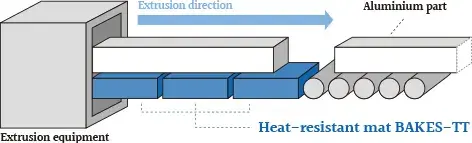
No damage on 500 degree aluminium parts and long lifespan
Couldn’t you choose BAKES used for steelmaking processes at higher temperatures than aluminium?

WY:There was a time I thought so too :) I tested BAKES with a lot of confidence, thinking that the existing BAKES is perfectly heat-resistant and used as roller bearings to roll out 1000℃ steel, so why not for aluminium? I failed big time. Aluminium products from the extrusion process were so much softer than I had imagined, and as soon as the products went through BAKES made out of hard phenolic resin, the products were damaged. I realised that the BAKES had to be much softer than the previous ones. Thus, I decided to develop a product that is not made out of resin, which is Starlite’s expertise, but of fabric with some tweaking.
Do you worry about or are you afraid of breaking the precedent?

WY:As I developed, I came to learn that fabric is the best, however, we had no experience in dealing with such products in BAKES. “How do we mass produce?!” “How are we going to manage quality control?!” There were worries one after another, but Leader I left me, opps, gave me a supportive push, saying “If you have a good feeling, then trust and go for it! Leave mass production to me!” That made the team feel we must succeed no matter what! It was really reassuring.
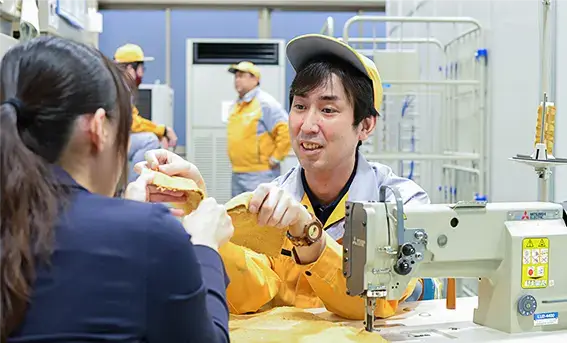
This is the finished product, BAKES-TT! It is real, not resin. Are you sure such a soft feel is robust enough…?

WY:Actually, soft and heat-resistant felt (sheet) had been used in the aluminium extrusion processes, but they were only made out of short fibres (Figure A) and it frayed with use. If the felt is hardened with resin, the fraying will be reduced, but it will still damage aluminium parts. I asked myself, “how do you harden the fibres”? The answer was to “harden by weaving firmly.”
In BAKES-TT, the continuous fibres are tightly aligned by multilayer weaving (Figure B). It can be used 8 times longer than the heat-resistant felt and the replacement frequency and waste have been significantly reduced. In other words, a cloth (woven fabric) mask can be used repeatedly for longer than a non-woven (felt) mask.
Figure A Felt
(easy to fray)
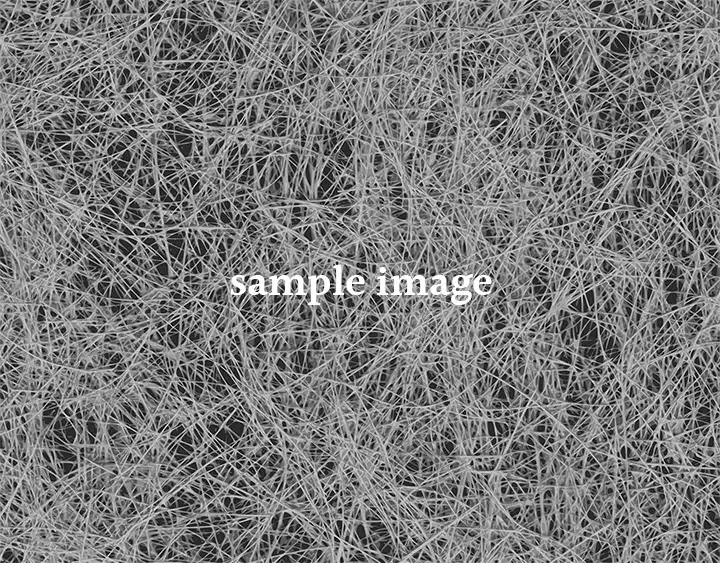
Figure B BAKES-TT
(Multi-layered, not easy to fray)
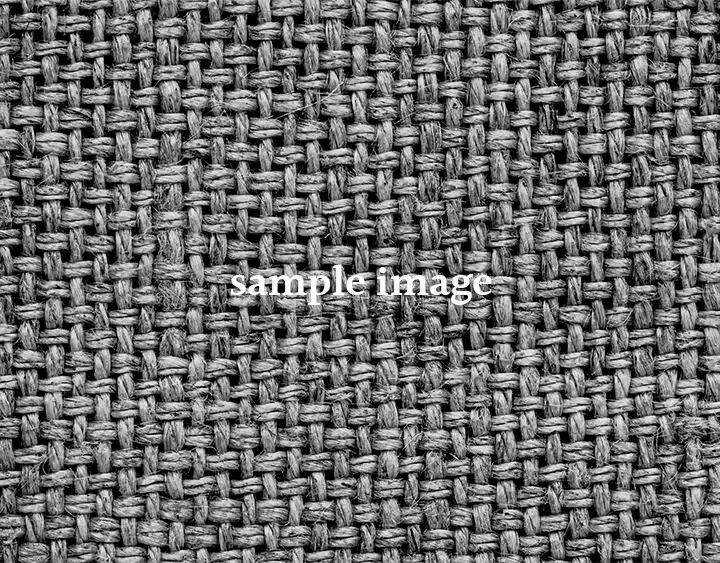
BAKES-TT is a revolutionary new product that is easy on the workers, the environment and your wallet! What is next for the team “Destruction and Creation?”

WY:The development of super heat-resistant products for industrial equipment and devices is a constant focus. With the tribology technologies, Starlite created “products that can be used for a long time without wear” and “products that can reduce damage and the loss of energy by eliminating friction” up until now. However, from now on, we plan to propose more BAKES products with sustainable viewpoints, such as “repeatable and recyclable” or “made from biomass materials”.

IH:You are summarising so well, but isn’t there a chance for me to speak?!


WY & SW:Sorry, but out of time :)
Interview Summary
This time too, they continuously betrayed me in a good way. Each of them are doing what they are good at and enthusiastically working towards the goal to find solutions. That is what we call ONE TEAM! Starlite is supported by a team of people who aim to break through various narrow gates. I will keep discovering these CREATORS!!
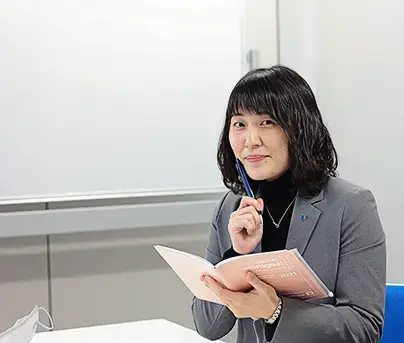
We look forward to working in partnership with you!
BAKES-TT can protect soft aluminium extrusion parts. Not only is the product life 8 times longer than existing materials, but it can also be collected after use and unused part of the sheet is recycled. Starlite continues to develop and propose sustainable products and services for this planet. Please feel free to contact us.