STARLITE CREATORS Vol.7Do not get stereotyped! Starlite’s Moldmaking Technology
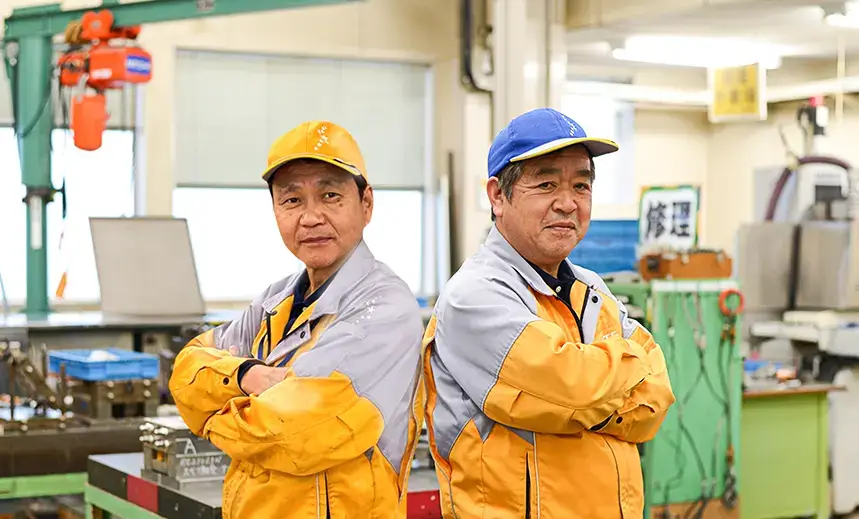
Starlite’s creators on the front line were all amateurs at the beginning. I wanted to know how each person built up their careers and trust over years! Today, I want to focus on the most important item in Monozukuri (manufacturing), “moldmaking technology”. If they are IKEOJI (young at heart), there is nothing that stops me from going. The first creator is OS who has been in the moldmaking section at the Ritto plant for over 30 years. You would never guess from his gentle smile that he is a fierce fighter who has been through a lot of hardships. Let’s ask about the difficulties of mold design and how rewarding it is…!
Mr OS, can you please tell me what the “mold” is?

OS:I am so pleased young people like yourself are interested in molds. ;)
In plastic molding, the resin is molded into the form of a product. I am responsible for injection molding which requires sturdy metal molds because the resin is poured into the molds at high pressure. If the mold is not good enough, the product will never be good no matter how good the materials or design technology are. It is our responsibility to maintain and always keep the best condition of the mold which is indispensable in Monozukuri (manufacturing).
Molds are the key! Resin Injection Molding
The melted resin is poured into the mold to make the shape of a product. If you only hear that, it sounds easy! (sorry)

OS:No, not really! There are more than 100 types of resins and each has different properties and thermal behaviours. Not only design technology but also the ability to make proposals based on material technologies are needed for the resin to perform its best. For example, deformation and other defects occur due to shrinkage change after forming caused by resin flow in the mold or the way resin hardens. It is therefore essential to set forming parameters based on resin properties and design molds whilst considering shrinkage.
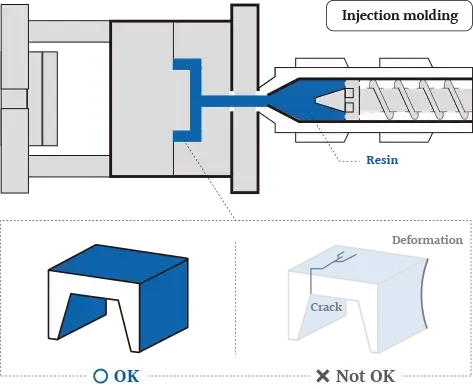
Possible defects on formed products are thought through and molds are designed to prevent those defects from occurring. When you have been working on molds for years, you must be in love with them!

OS:It has been more than 30 years since I started looking after molds. The first plant I worked at was Nasu Plant (used to be in Tochigi, but it is permanently closed). Due to a significant increase in production, my subordinates did not have time to teach me and I was left on my own. What I did then was to work at a tool manufacturing company even though I was fully aware that I would be disturbing their work. I asked a lot of questions persistently, which helped me to develop my design skills. I could not understand any of the terminologies, but they educated me without making me feel uncomfortable. I still appreciate them.
I realised my skills had improved when we were not able to eliminate burrs on a mold regardless of numerous refurbishments and I went to the customer to apologise for them on my own. I was prepared they would strike a hard blow, however, I explained everything honestly without hiding anything. The customer then came up with an idea, and from there, it did not take too long for us to produce OK parts. I was amazed and grateful throughout. After all, it is through people outside the company that I was able to learn and grow a lot. It is ideal to have a relationship to rely on and to be relied on. It is like having mental support and it makes me feel “everything will be okay!”
- Burr: It occurs when resin material seeps through a gap of the mold. It is an unintentional protrusion.
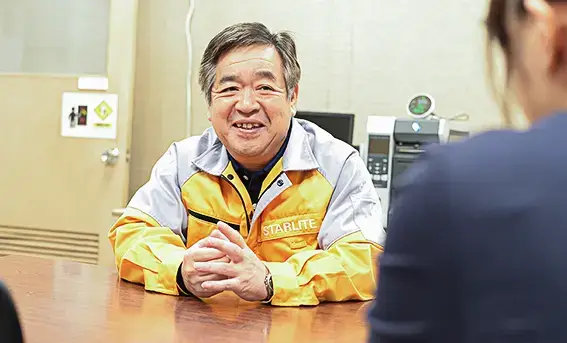
You have worked on molds for various products.

OS:I have a broad range of experiences from a frame case of a photocopier to a fingertip-sized precision component. For some reason, Starlite is very good at collecting orders for difficult products that other companies gave up making. Thanks to that, I was able to have a lot of experiences :) For example, it did not take too much time for us to make a part that was 20 times thicker than conventional formed parts. I heard at a later date that another company tried for more than two years, but they were not able to make it. I was asked repeatedly, “how did you manage that!?”
But of course, I do worry. We issue a fixed drawing, but we repeatedly ask ourselves “was this the best drawing we could have issued?” until the moment the mold is manufactured. If we make any mistakes, it will take time and money.
Is mold design a gamble…?!

OS:Possibly it is. A subtle yet bold decision is needed. Now I am confident that I will not lose that bet. However, before reaching this point, I refurbished molds over and over again. It cost us money worth building a new house...
Until a product is molded, it is not clear if the mold is okay or not. Toolmaking and modification costs are very expensive and larger mold would cost up to tens of millions. To make an OK mold, not only do I still talk to many people, but I also dismantle and assemble the mold to understand its structure and use forming simulations to verify my findings rather than relying on my experiences alone, etc. I am always looking for the best possible final answer.
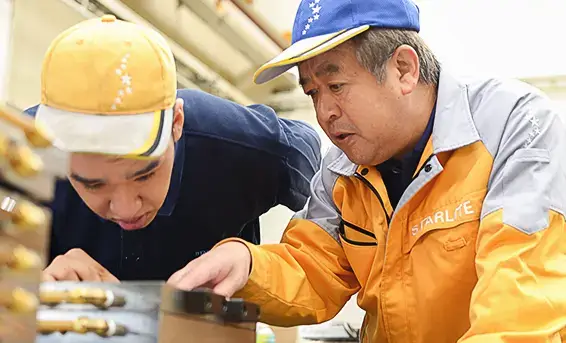
The largest size of molds that OS is responsible for are about the size of an office desk, but FI from Hiroshima Plant, whom I am going to introduce next, is responsible for molds that are the size of a small car. They are used to make automotive parts! Every time FI sees cars, he cannot help looking at internal/external parts that he is making…

FI:Every time I go to a showroom to see new cars, I still get excited, saying “That’s the part I made!” I then spend a lot of time observing the finished level of other company’s plastic parts. The mold design has a significant impact on the quality and appearance of a part. Where is the weld line?? what is the gap between the molded part and the connecting part?? etc…
Weld Line
: It is the line where two flow fronts of melted resin inside the mold meet during injection molding. It is necessary not to make this line too visible on molded parts that require a good appearance.
A lot of plastic parts are used for cars nowadays. FI has been manufacturing molds from the early days.

FI:There is a process in which an image by the designer is transferred to mass production designing. Back then, there were not many engineers who could design products for resin material at automotive manufacturers. That is why we were approached because we were mass producing large-sized resin products such as bathtubs.
The customer is not a resin expert and Starlite had little automotive knowledge. Were you able to communicate?

FI:We did not discuss by just looking at the part on the table. We thought about the balance by looking at the entire car together and exchanged ideas by working at each other’s factory. A lot of internal and external parts are visible from drivers. Therefore, it is necessary to make an intuitive judgement for colours and quality which is more than the numeric specification. The condition of the mold will have a significant impact on how the colour is shown and the feel. Therefore, we shared the concept of values together and repeatedly asked ourselves “Couldn’t we make it any better?” When the product was not within the specification, I had days that I dreamt of myself worrying in front of the product, that I felt the customer’s factory was at a far distance on the reporting day, etc.
Once we started making some progress, we began making proposals in which the customers’ requests were already reflected before they made a request. That was when the “Design and Development Section” in charge of doing that and “Tooling & Engineering Section” in charge of making molds for mass production were created.
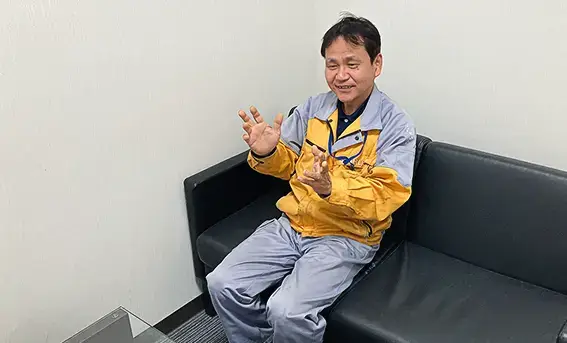
Finally, what is the most important thing in Monozukuri (manufacturing)?

FI:It may sound old-fashioned, but it is a relationship with customers. About 10 years ago, Thai Starlite (oversea operating site in Thailand) had a defect on a mass production mold and contacted me, saying “the customer is very angry. Please can you come and help us?” When I arrived in a big hurry, the customer, with whom we have had a long relationship in Japan, was waiting and smiling at me. I was invited to a dinner by the customer the night before I returned to Japan and he said “If I snap at Starlite, I thought you would come and solve it somehow. Thank you.” I thought it was a bit of an exaggeration but we were able to start mass production as scheduled, which was good. How people connect to each other has become diversified, however, I still feel it is important to talk face-to-face.
Interview Summary
It is said, “Two heads are better than one.” Mold design is a pool of ideas and knowledge and it is tested by the rigours of people and supported by people. Nowadays, it is possible to gather ideas about mold design from various locations online, but there are many items that cannot be discovered on screen. I think it is quite obvious when I get infatuated with IKEOJI (on-screen) though :)
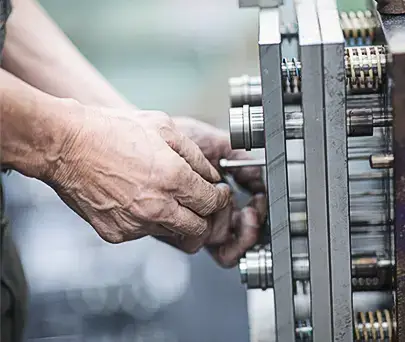
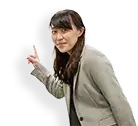
Products made from Starlite mold are
used around the world! I am so pleased!
Please
swipe
We look forward to working in partnership with you to create new solutions.
STARLITE has responded to the needs and challenges of plastics in the industry. We will continue to improve our mold design technology and develop more reliable products for our customers.