STARLITE CREATORS Vol.10Customers are amazed at how thin Starlite's resin gear reducers are! It also saves cost! A closer look at a group of pioneers who has created the resin gear reducers that contribute to "automation"
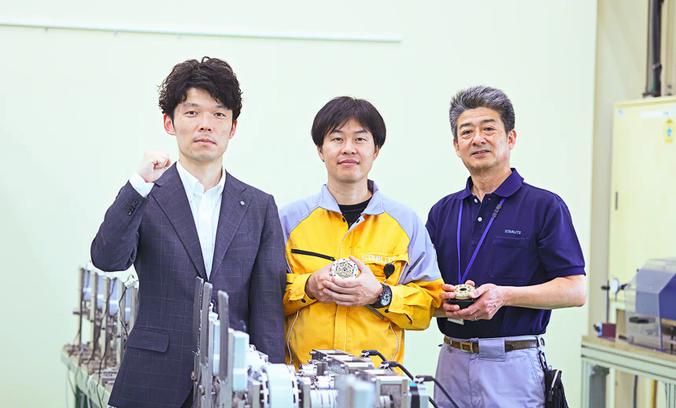
Good afternoon, I am Hanaoka from Public Relations and this is my first time to do an interview for the Starlite creators. I am a bit nervous because I tend to let my emotions show on my face when I cannot keep up with conversations.
Starlite's resin gear reducers have been used on electronic locks for housing equipment and photoconductor drums in multifunction printers, and Starlite is expanding its business into the robotics industry, conveyors and carriers, and electric bicycles. Now let us meet the team!

Team of resin gear reducers
M.TSales promotion leader. He is a team leader who can be counted on to gets things done when needed.
O.NMember who designs and tests reducers. Once he decides to do something, he is determined to see it through until the end, and is always eager to explore unknown areas.
K.KMember who designs reducers and molds, and establishes assembly lines. He is an experienced engineer who has overcome many obstacles in mass-production.
Development of resin gear reducers has started.
I hear Starlite has launched the development of resin gear reducer units based on the results of mass-production of the highly durable S-Bear® gear, Starlite's original material.

M.T:Yes, the development was started in 2003. I joined the project as a sales promotion member in 2019. In the beginning, I could hardly follow what O.N and K.K, who both are highly experienced, were talking, and I had a lot of catching up to do even when taking meeting minutes.

O.N:M.T is a really hardworking person. He attentively listens to customers and is capable of carrying out effective conversations. His responses with full of technical insights are well received.

K.K:M.T clearly explains what customers said and what he picked up during the meetings with customers. So we can have deeper discussions.

M.T:No, no. There are many things I still have to learn. For example, the development of the internally-toothed gear reducer that is a small module O.N had worked on.
What is a reducer?
It is a unit that reduces with gears the torque produced by power source such as motors, and generates stronger power.
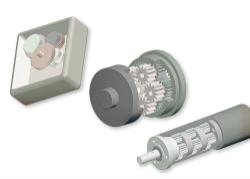
What is S-Bear®?
S-Bear® is a high-performance engineering plastic materials developed for injection molding, using Starlite's tribology, material design and material production technology.
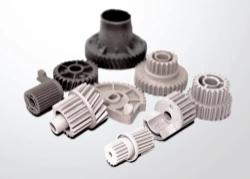
Behind-the-scenes story of the development of reducers for office multifunction printers
Oh, what is it? Please explain as you talk to someone like me who joined the company a couple of years ago.

O.N:Office multifunction printers are equipped with a photoconductor drum that transfers toner to paper driven by a reducer. The goal was to reduce the cost by using resin to manufacture reducers that had been made of metal. Before starting the project, we first presented our customer with a 15-page proposal of what it should be based on. They agreed with the proposal and to work together. It was good until we began the development process and then we had a lot of challenges for the first two and half years. What our customer wanted was a ultra-compact reducer unit having the differential planetary gear mechanism with 30 mm outer diameter. Precision must be at the same level as the existing metal products.
30 mm outer diameter is just the size of the PET bottle lid.

M.T:Yes, it is pretty small.

O.N:After our fourth prototype was unsuccessful, we tested two of the differential planetary gears separately and found that one of them was actually better. We did not see the difference because we had only tested them in the assembled state. When we built other parts in the same way as the better one was built and saw the measured data, we were convinced that we can do this! We later found out that our customer was thinking it would be our last shot.
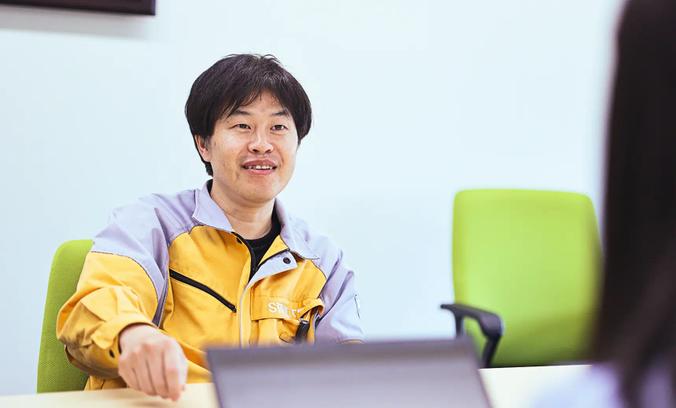
You took the last opportunity and nailed it!

O.N:Our design process went smoothly after that, and the next step was to mass-produce, but…

M.T:That must be the major obstacles we often hit during the development stage.

O.N:The tolerance for mass-production was extremely tight. It was pretty difficult to perform the maintenance, let alone produce the molds. When gas components formed during injection molding build up in the mold, it causes variation in precision. By collecting more detailed data, we made forecast management that catches the sign or tendency of worsening in precision and does maintenance ahead of time, instead of measuring the products and performing maintenance after getting close to the tolerance limit.

K.K:Members in the production lines were very proactive and the good teamwork between the development team and the production line team led to improved quality control.

O.N:I asked my customer about the initial production control and they said they wanted me to take charge. Encouraged to do our best, we created a process based on the mass-production data ten times more than usual and my customer developed dedicated assessment software. There has been no complaint received from the market thanks to everyone's efforts.
All these efforts you made have paid off.

O.N:I am grateful to my customer who was struggling with us through to the end. A senior engineer whom I had hardly seen at customer meetings said to me in tears, "The mass-production of this product is going to make history. Thank you very much!" I realized then that he supported this project behind the scenes. I am filled with gratitude.

M.T:Our veteran K.K, who told me about the development results of the S-Bear® gear, was also involved in the development of the electronic locks with super-thin differential drive reducing mechanism.
What is the differential drive reducer?
With the originally developed two-staged planetary gear mechanism, high reduction to 1/100 is achieved with a single gear. We have created reducer units that are thin, lightweight and cost effective with Starlite's precision injection molding technology.
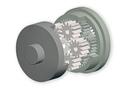
Configuration of S-Bear DD4830
Are the electronic locks used to open and close hotel rooms and house doors with a card or smartphone?

K.K:The existing reducers for residential door locks were huge and poorly designed. We then came up with an idea of reducing the thickness and size as much as possible, which can make house door design look more attractive.
Behind-the-scenes story of the reducer development for electronic locks
How thin was the resin gear reducer that you have proposed to your customer?

K.K:We have made it 7 mm thinner than our customer expected.

O.N:Our customer was very excited about how thin it got. Besides, K.K was so quick to design that it took him just a week to finish.

M.T:Really? That is fast. K.K is not only quick what he does but also is in charge of developing and testing the prototypes.していますよね。

K.K:After the development started, our customer’s requests got tougher and tougher. For example, they wanted higher efficiency on the reducer's side to compensate for the decreased power of the motor that drives the reducer, they wanted us to find substitute parts even though we wanted to use other particular parts to lower the production cost, etc. Because this was the first time to mass-produce with differential drive reducing mechanism, it was challenging to embody the theory. It was like we were lost in a maze for a year and a half. Every time we come up with an idea, we tried hoping to get it right. All the things I tried during this project became the foundation of my ideas today.
How was it like for Starlite to develop reducers for electronic locks for the first time?

K.K:Our knowledge of quality control for expected problems with the electronic locks was poor, but we learned a lot through this project. When the first mass-produced reducers were about to be shipped, we knew everything was in good order but we were so nervous that we had to unpack the package to check one more time. It was a nerve-wracking moment.
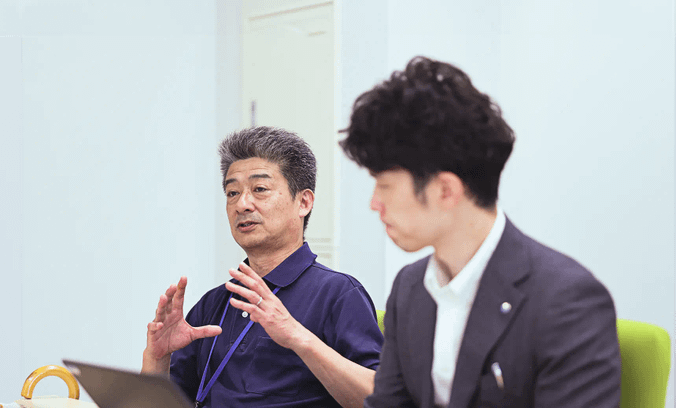
That does not sound like K.K who has extensive experience.

K.K:We focused on the design that does not cause misassembling of the reducers and always stay on our toes until the shipment is delivered. There are of course no complaints from the market.

M.T:I did not know there are such moving stories of the two resin gear reducers which are displayed in the permanent exhibition area of STARLITE Exhibition Hall. In our next project, we should start a new story together.
Resin gear reducers support the working-age population
What will the marketing plan for the resin gear reducers be, M.T?

M.T:As part of in-house project, we have launched a motion engineering project and the resin gear reducer is the key product. The decline of the working-age population in Japan has recently been a serious issue, but we think that the "automation" of production lines will play a more important role. We believe that not only production lines but familiar applications will require automation to achieve both safety and mass-productivity without harming people. We are convinced that our resin gear reducers can contribute to solving the issue.
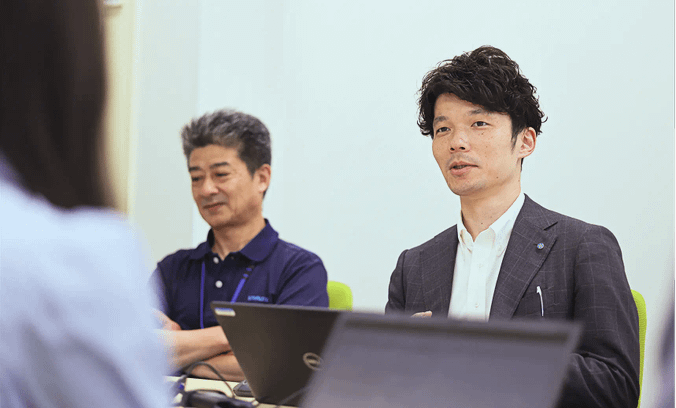
Interview summary
Before this interview, I thought Starlite focuses on parts such as high-performance gears and bearings, but also develops unit products that draw out the potential of those parts. I realize our CREATORS are the professionals who never give up and keep pushing forward until our products bring joy to customers. We should keep our eyes on the next CREATORS like M.T!
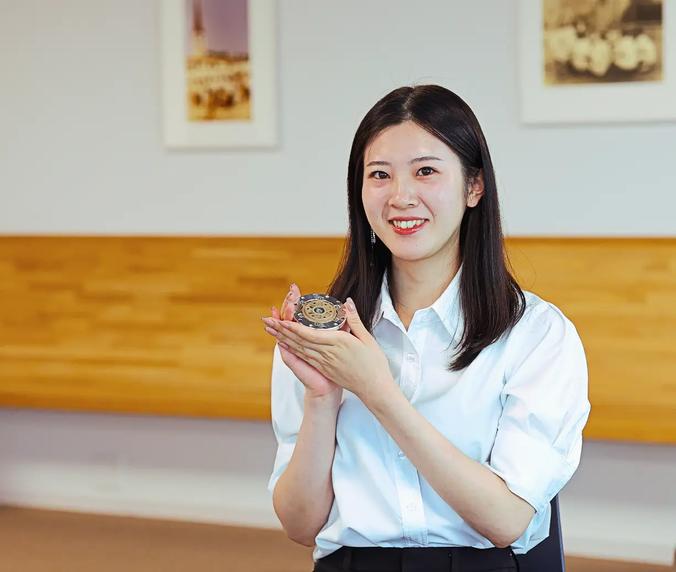
We look forward to working in partnership with you to create new solutions.
Starlite's resin gear reducer design can be customized for such as special underwater applications, greaseless use, flatness, small diameter, compact and high reduction ratio. Please feel free to contact us.