STARLITE CREATORS Vol.11クルマづくり特集 Vol.1不具合流出3年ゼロ!自動車産業を支えるCREATORSと最先端工場がつくるミライ
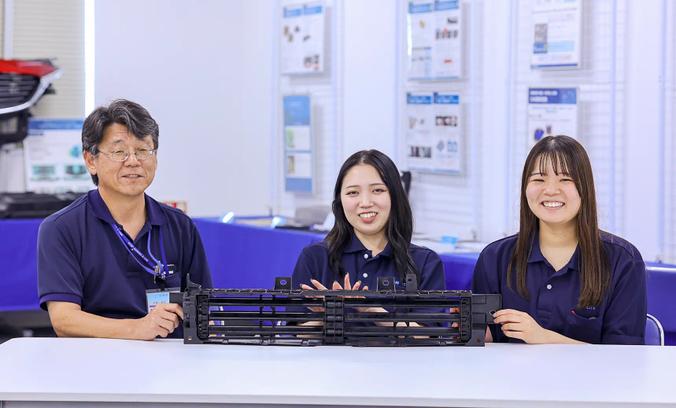
こんにちは。広報担当の花岡です。突然ですが、スターライトは自動車の重要なパーツを作ってるんです!と高らかに宣言させてください。多くの課題を乗り越え、自動車の性能を改善し続けるCREATORS。そんなみなさんの熱い「クルマづくり」を特集として、全4回でお届けしていきます。
第1回目は、自動車の高性能化に貢献するユニット製品「AGSことアクティブグリルシャッター」などを生産する山口工場に突撃!早速、山口工場を立ち上げたCREATORSと、次世代のCREATORSにお話を聞いてきました!
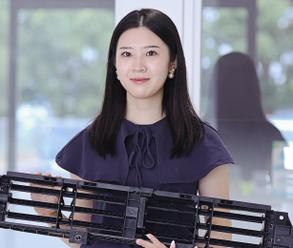
Y.K山口工場創業の第一人者。山口工場の「なりたい姿」をとことん突き詰める。
Y.M副資材などの手配を担当。生産を支えている。社会人4年目の頼れる先輩。
U.M社会人3年目のムードメーカー。生産計画を担当している。
山口工場は2018年設立の新しい工場ですよね。

Y.K:うん、主に自動車向け製品を、約25年間生産していたグループ会社をベースに設立された、最新鋭の工場ですね。
ここで生産している「AGS(アクティブグリルシャッター)」って何でしょうか?

Y.K:ビジネスパートナーのドイツ企業「ロシュリング・オートモーティブ社」とスターライトが世界に展開する自動車には欠かせない製品のこと。ラジエーターグリルの後ろにあるユニットで、エンジンルームへの外気流入をコントロールして、暖気時のエネルギーロスを減らす役割が....あ、難しいかな? とにかく、空気の流れをコントロールして空気抵抗を減らし燃費向上につなげる役割もあって、大注目のユニットなんよ。
AGS(アクティブグリルシャッター)
そんなAGS生産のためにすごい射出成形機があるとお聞きしましたが…。

Y.K:国内最大級1,850トンの2色射出成形機やね。
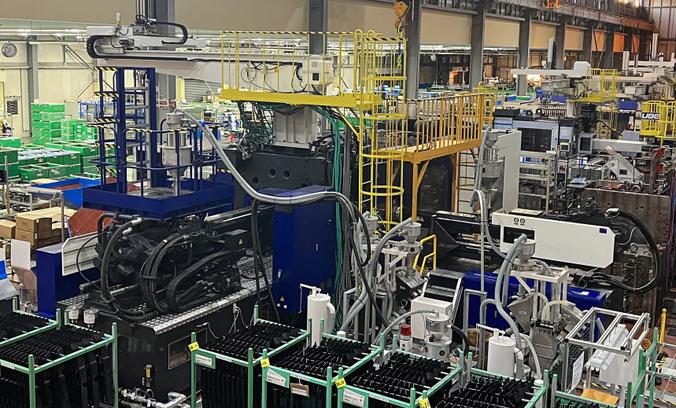
国内最大級!なぜ、2色射出成形機が必要なんですか?

Y.K:AGSの構造は大きく2つに分けられる。バンパー開口部からシャッター部分へエアを導くエアガイド部分と、そのエアの出入りをコントロールするシャッター部分やね。シャッターのフラップはモーターで動かすから、そのフレームはゆがまないように硬い材料を使っとるんよ。
逆に、エアガイドはバンパー開口部の裏側に密着するように柔らかい材料を使ってる。大型の硬いシャッター部分と柔らかいエアガイドのフレーム部分を、2色成形機やったらいっぺんにつなぎ目なしで成形できるから、エアの漏れを防げるようになっとるよ。
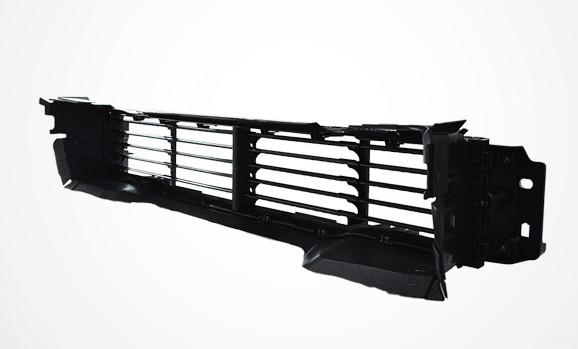
2色射出成形機で1度に成形できるから、手間も省けて性能もアップなんですね!

Y.K:そうなんよ。2部品を別々に作り、その後でつなぐよりも、効率的で効果的と言うわけ。ちなみにAGSは量産開始から現在まで、3年間の不具合流出はなんと0件!こんなに複雑な構造の大型成形品を、それも複数個取りして安定生産しているのはうちだけやと思うよ。
不具合もゼロ!安定生産を支える最先端工場なのですね。山口すごいですね!

Y.K:それだけじゃないんよ。外観不良を改善する射出成形だったり、インライン生産方式だったり、協働ロボットによる自動化もやっとるんよ!
気になるワードが次々と…。まず「外観不良を少なくする射出成形」とは?

Y.K:金型を締めるときに、まず柔らかく締める。金型への樹脂の流し込みにあわせて、金型が開かないように段階的に高圧で締めていく。樹脂が溶けて発生するガスが金型に残ってしまうと製品表面の外観不良の原因になる。ガスを逃がすわずかな隙間をつくりつつも、そのあとに流れてくる樹脂のはみ出し不良(バリ)をつくらない、そんな射出成形技術のことやね。射出成形機のコントロールはもちろん、金型にもノウハウがある。もし樹脂のはみ出しが金型にまぎれ込んだら、連続成形がストップしてしまったりするんよ。 金型担当者の記事はこちら
外観不良を防ぐ金型技術
ユーザーからまる見えの自動車の内・外装品は、外観不良対策がすごく重要ですよね。

Y.K:山口工場は効率を重視したモノづくりも進めてて、例えばインライン生産方式とか。
気になっていました。詳しく教えてください!

Y.K:成形加工エリアと組立加工エリアがワンフロアでつながっとって、射出成形機から一本の線で物が流れる体制のことやね。かつ同時化生産もしていて、組立も成形機の横で完成させている。2023年11月にAGSも成形機の横で完全に完成させるようにしたんやけど、成形と加工をこれからもどんどん引っ付けていきたい。
モノの移動が最小限で済むので、すごく効率的ですね!

Y.K:作業員をアシストする「協働ロボット」もうまく活用してるよ。初心者や実習生とかが入っても安定した組立ができるようになってるね。単純作業はどんどんロボットに任せているから、少人数のモノづくりが徹底でき、新提案とかテストに人の時間が使える。大きな成形品に細かい部品を組み込む作業は体力的にもきついし、品質の安定化もしづらくなる。そういうところを協働ロボットに任せているよ。
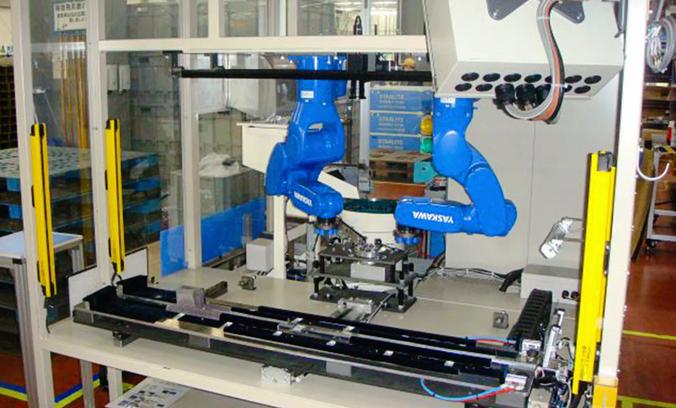
すばやく動けて、疲れ知らずの優秀なアシスタントですね!

Y.K:人と協働ロボットが組み立てた完成品は、AGF(無人搬送機)が出荷場所に持っていってくれる。今、試しているのは、射出成形品の自動取り出し機から直接、協働ロボットにバトンリレーすること。ちょっとでもつかみ位置がずれると落としてしまう。でもこれができれば、完全自動化にかなり近づけるんよ。
カウルグリルという、車の横幅ほどある大きい製品の収納ケースを運ぶ台車があるんやけど、それを「AGV(自動走行台車)」で自動搬送するというのも始めたよ。原料の保管置場から、紙袋に入った原料を成形機サイドへAGVで移動するという取り組みもチャレンジ中。そして、皆さんもご存じのファミリーレストランの配膳ロボットを利用して、副資材を組立加工ライン(作業台)に移動させるチャレンジも行っているね。
製品の生産から出荷までの流れ
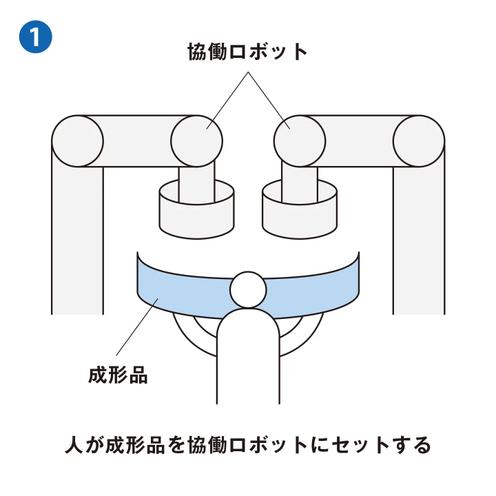

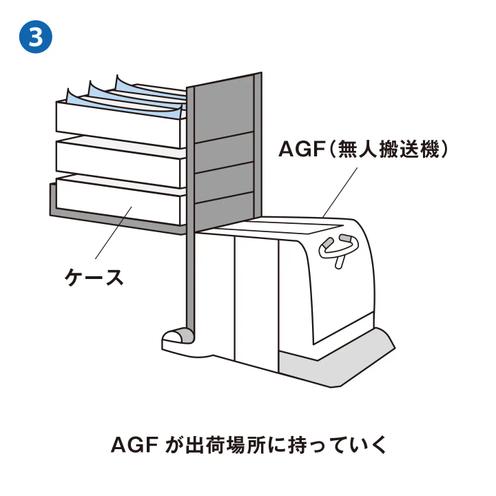
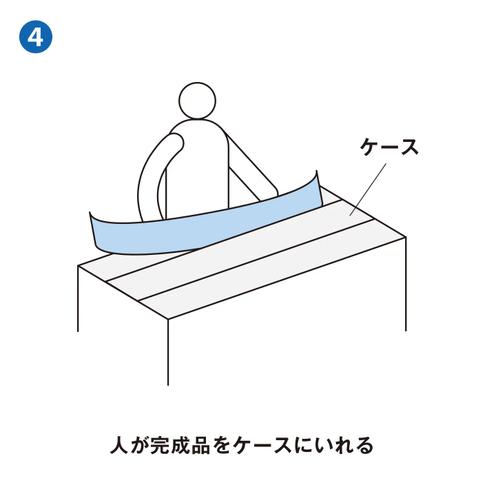
横スワイプで続きを
次々と効率化のアイデアがあふれていますが、その想いの源とは何でしょうか?

Y.K:人が持っている能力を活かして付加価値の高い仕事をしたいというのと、山口工場の設立コンセプトである「魅せる最先端技術によるモノづくり工場」に向かって、前進していくためやね。人手不足だからって夜勤シフトに作業者を補充するだけでは固定費が増加して、収益悪化するだけ。人が集まりにくくなってきている状況でもあるから、それを回避したいという理由もあるけどね。
人の知恵で工場を進化させて、より良いモノづくりをしていきたいね。

「魅せるモノづくり工場」に向かってどんどん進んでいますね!「無駄」や「非効率」に気づくアンテナの感度がすごく大切ですね。

Y.K:生産現場だけでなく、工場の要である生産管理の方でも、DXの取り組みがスタートしたね。例えば出荷確認では、製品についたバーコードを自動で読み取ったら消し込みできるようにしている。ほかにも、各成形機に工場内のすべての成形機の状況が分かるモニターを設置し、トラブルや稼働状況がひと目で把握できるようにしていきたいね。

U.M:おーいいですね。

Y.K:持ち運べるタブレットでもその状況が共有できるので、変更されたことがどこにいてもわかる。

U.M:おー、それいいな、それいい。歩かんでいい、歩かんでいい。

Y.K:組立完了の確認もバーコードを読み取れるようにして、その状況をモニターで共有すれば、遅れていないかの進捗とかも全部現場のどこでも見えるようになる。

U.M:いいですね。1時間おき、2時間おきぐらいに生産現場に行っていたのが、事務所の机にいても生産のすべての動きがタイムリーにわかるようになるんですね。おー、楽ちんですね。机でやらなきゃいけない仕事に集中できますね。

Y.K:とはいえ、生産現場を見て回ると、改善のネタだったり気づきが見つかるから、座っているだけじゃよくないね。
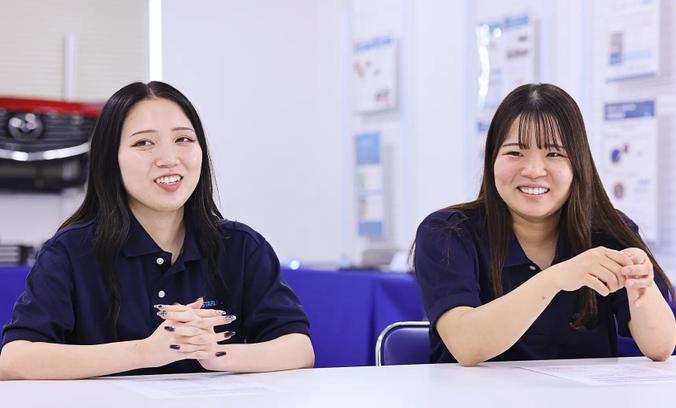
そういえば、山口工場って、敷地にまだまだ余裕がありますよね。

Y.K:そう、第2工場の建設の絵も描いているよ。いつでもスタートできるように構想図も作って、建設費も概算費も調査済み。水の循環システムも取り入れたいと考えているね。
「水の循環システム」とは何ですか?

Y.K:射出成形の金型を交換するときに、金型の中に溜まっている冷却水を全部出さないといけないんやけど、それが金型1面あたりだいたい40~60リッターにもなるんよ。それを一度使って終わりではなくて、回収してぐるぐる再利用できるようなシステムをつくっていきたい。

U.M:もったいないですもんね。使い捨てじゃないほうが良いにきまっとる。第2工場には私たちもどんどんアイデアを出せるようにしないといけないですね!
これからの山口工場を担うお二人ですもんね!U.Mさん、Y.Mさんの夢や、してみたいことなどお聞きしたいです!

Y.M:例えば、ボタンを押すだけで、違う場所にいる人とすぐに話せる仕組みがあったらいいなと思います。第2工場ができたら、第1工場と第2工場の行き来で時間ロスになるので、いつでもどこでも顔を見て、しっかりコミュニケーションを取れるのはすごく便利ですね。頼みごとや連絡事項があるときとか、表情やしぐさが見えたほうがしっかり伝わるし、結果的に仕事のスピード感も高まりそうですよね。山口工場の人だけでなくて、他の拠点にいる人だったり、海外にいる人とも顔を見て話せる仕組みがあるとおもしろいですね。

Y.K:うん、大型モニターに向かって話しかけたら、各場所にいる人と画面上ですぐ話せるとかもいいかもしれんね。相手がちゃんとわかるほうが安心できるし、そのついででいろんな情報交換ができてコミュニケーションも増えそうやしね。
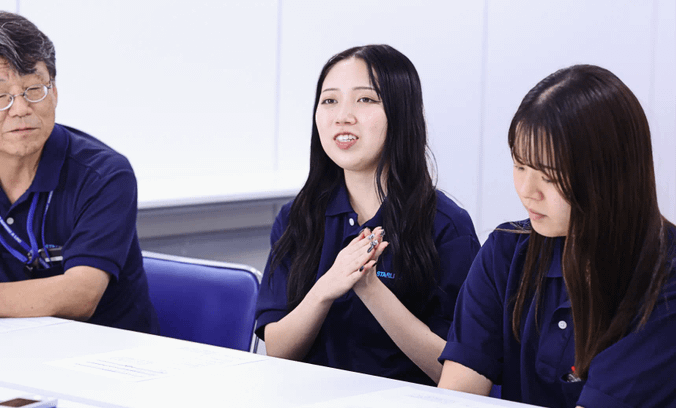
デジタルをうまく活用して仕事も効率的に、コミュニケーションも活性化して、どんどんアイデアが出てくる場にしていきたいですね。

U.M:私はスターライトのブランドカーを、山口工場で一からつくれたらおもしろいなあと思います。19km/h以下だったら比較的自由につくれるみたいなので、第1工場と第2工場を移動できるモビリティとして使えれば便利ですし楽しいですよね。
スターライトは超軽量の次世代モビリティの搬器を試作しているので可能性大ですね!

U.M:ブランドカーは何かのキャラクターの形とかにするとおもしろそうですよね。私は「おぱんちゅううさぎ」がめっちゃ好きなので、その雰囲気のモビリティに乗ってみたいです!そのキャラクターもひとつだけじゃなくて、いろんなキャラクターのものがあったり模様替えできたりしたら、見てて楽しそう!
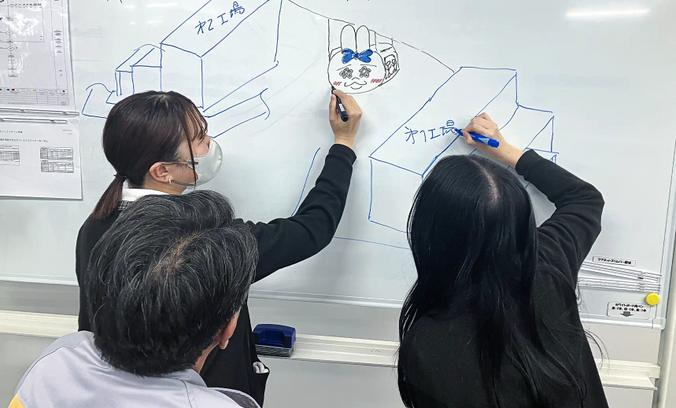
わー、元気がもらえそうで、いい気分転換にもなりそう!

Y.M:モチベーションを上げるためにも、制服を自分好みでカスタマイズできるといいなあって思います。ロゴだけ統一にしてカタログとかでデザインを選べたりすると、自分好みの服が着れるので気分も上がりそうです。お客様にお会いするときは正装で、っていう使い分けをしたらいいですよね。私は黒とかクールに締まった感じの制服が着たいです!

U.M:楽しみながら仕事ができれば自由な発想も生まれやすいと思います。おもしろいアイデアをどんどん出していけるような環境にしていきたいです!
したいことが盛り沢山!いろんな意見で溢れる工場として更に進化しそうですね!

Y.K:モノづくりはもちろん、新しい働き方も提案する「最先端の魅せる工場」として、いつかはみんなに「山口工場こそスターライトグループのマザー工場だ」と言ってもらえるようにしたい。
現在のマザー工場である栗東事業所を超えていくなんて、メガ進化じゃないですか!

Y.K:そうやね。栗東事業所でやっているスーパーエンプラ材を使った製品の生産なんかもやりたいね。耐熱性や強度が金属並みに優れている材料なんやけど、成形はとても難しい。でもどんどんチャレンジし、栗東事業所を超える工場になっていきたいね。

U.M:新しい仕事をどんどん奪い取って奪い取って(笑)。みんなが喜んでくれる製品を山口工場から世界に出していきたいです!
インタビューまとめ
2018年に操業開始の山口工場では、これからできる第2工場での新しいアイデアもたくさん聞くことができてわくわくしました。まるで、近所の大人と夢いっぱいの子どもたちが楽しく語り合っているようで、見てるだけで幸せな気持ちに。自由な考えで盛り上がれるって素敵で、終始あったかい雰囲気のインタビューとなりました。まだまだ発展していく「最先端の魅せる工場」。これからの山口工場、ますます楽しみです!
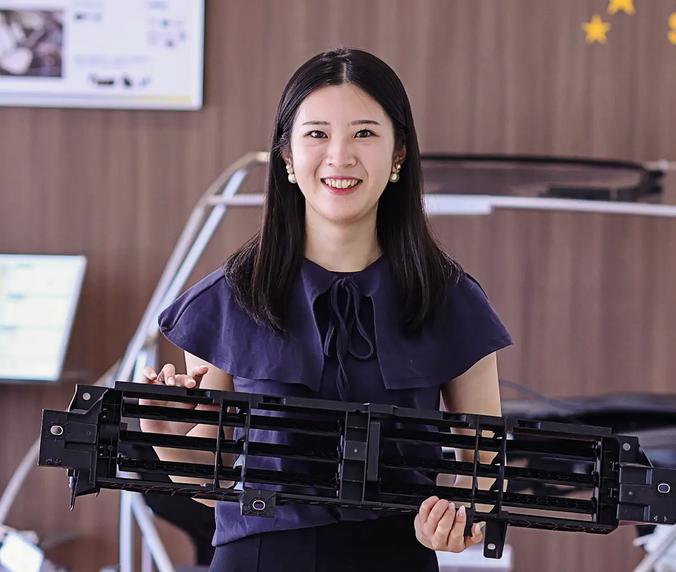
お客さまとのパートナーシップで新しい共創を。
ぜひご相談ください。
スターライトはAGSやカウルグリルなど自動車の機能商品を開発・製造しています。自動車の軽量化や歩行者保護、燃費改善などさまざまな課題に貢献しています。お気軽にお問い合わせください。