HIROSHIMA PLANT
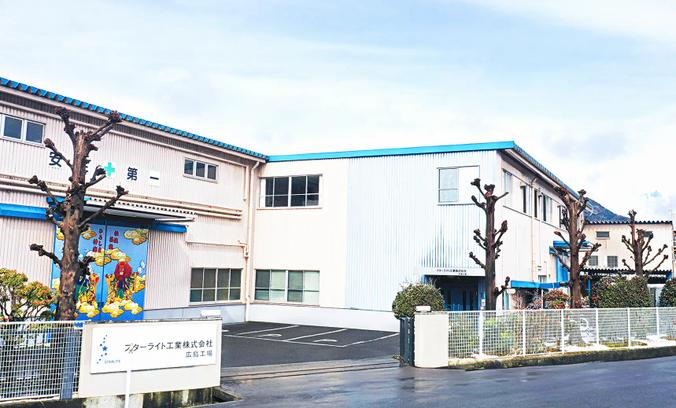
Hiroshima Plant, the production base for the Starlite Group's functional units for automobiles, was established in 1974 as a plant that plays a leading role in the Hiroshima area by bringing together know-how in mold technology and production technology, quality control and logistics.
The Plant is located in Akitakata City, Hiroshima Prefecture, where Koriyama Castle, the residence of the warlord Motonari Mouri, was once stood. Near the Plant is the Suga Shrine, which is associated with Motonari Mouri, who won many battles and is famous for his teachings on the legend of the three arrows. The shrine is known for Sanfrecce Hiroshima, a Japan professional football club, visiting the shrine every year to pray for victory.
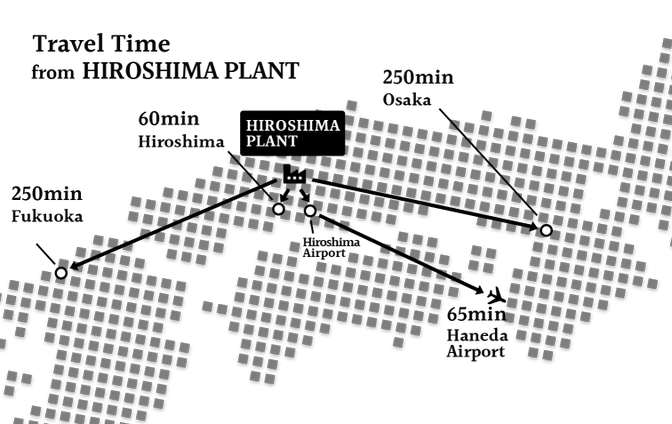
The name Sanfrecce is created by combining the Japanese word "san" (three) with the Italian word "frecce" (arrow). "Hiroshima Akitakata Kagura", a traditional performing art of Akitakata City, has been passed down for more than several hundred years since the Edo period, and the door of a building in the Plant is painted with the Kagura donated by the local Yoshida High School.
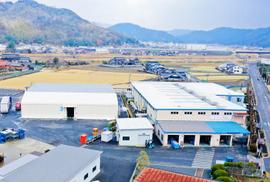
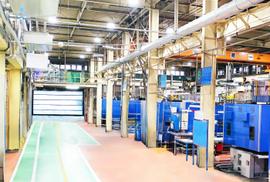
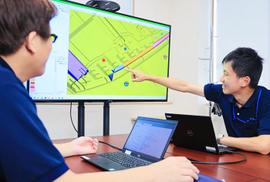
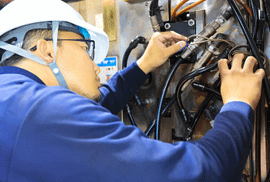
The main products Starlite manufactures are cowl grilles, active grille shutters (AGS) and sub tanks for automobiles. The cowl grille is an exterior unit that improves vehicle performance, reduces weight, and has a function that helps protect pedestrians. The AGS is a product that helps improve fuel efficiency by automatically controlling the airflow to the engine compartment and improving aerodynamics. We meet the various needs of our customers with functional products that also take safety and the environment into consideration.
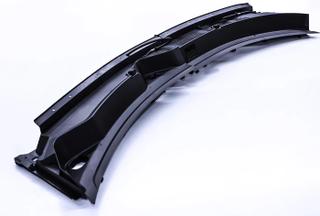
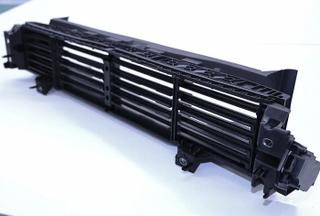
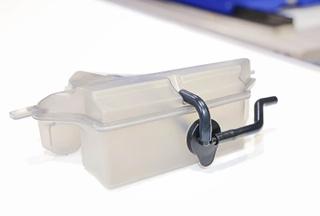
Initiatives in Production
The production at the Hiroshima Plant is characterized by the effective combination of production facilities and testing equipment, and the pursuit of production efficiency and quality assurance. We have a great advantage in our ability to work with the CAE team at the Development Center, which is responsible for functional development and product development, to expand a consistent production process for mold development, mass production, and delivery by the hour to our group companies in and out of Japan. In particular, our strength is that the mold development team is made up of a small number of selected members who can respond flexibly to each product specification. Our engineers, who have a wealth of knowledge and experience, are involved in discussions from the development stage of functional products and are always working to introduce and improve production processes that focus on quality and technological innovation.
Commitment to Quality
The Hiroshima Plant has established a quality management system based on the international quality standard IATF 16949 and has a quality assurance system that also conforms to the quality control standards of each automobile manufacturer. The Testing and Evaluation Center on the property is equipped with evaluation and testing facilities such as constant temperature and humidity chambers, weathering testers, and 3D measuring machines, and the highly specialized testing and technical teams work together to advance technological development and product prototyping. In addition to QCDS (Quality, Cost, Delivery, Service), we contribute to the stable production of high-performance, high-quality functional units for automobiles that are also environmentally friendly.
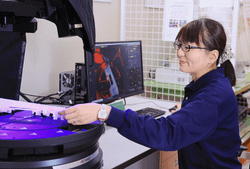
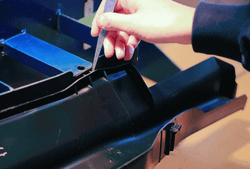
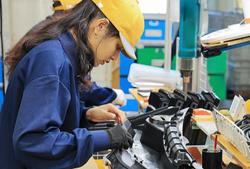
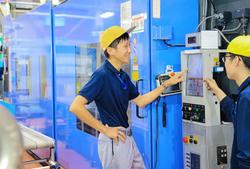
Commitment to Technological Innovation
For cars that emphasize design, functional parts with complex shapes are required. We have established a production process that combines the application of our long-standing hot plate welding technology with automation using robots, and we have already been continuing stable production for more than 10 years. The cowl grille, which has been designed using CAE technology to add impact absorption performance, is designed not only to maintain vehicle performance and reduce weight, but to prevent head injuries in the event of a collision with a pedestrian, protecting the safety of both drivers and pedestrians. The knowledge we have gained through the pursuit and accumulation of the latest technologies, such as the development of new production processes and digital engineering, is being used to promote technological innovation for the cars of the future.

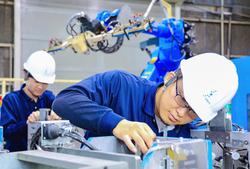
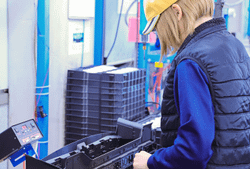
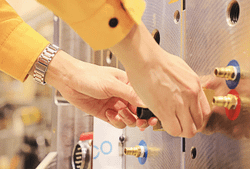
Our Messages
Manufacturing Section, Mobility Solutions Company
We promote the creation of a culture that values and fosters independence, and we work to encourage each member to act as if it were their own personal issue. Through the manufacture of functional parts for automobiles, we aim to achieve self-growth and make society a better place.
Manufacturing Section, Mobility Solutions Company
As the person in charge of quality control, building good communication with customers is directly linked to improving product quality. We try to communicate face-to-face, and always work to build trust with customers, provide accurate feedback, and respond quickly.
Back-Office Section
I work in the general affairs office, creating a comfortable work environment for employees. The work is diverse and there is always something new to learn every day. I feel a great sense of joy and accomplishment in creating a work environment that connects people.
Mold Engineering Section, Mobility Solutions Company
I oversee the management of the mold engineering section for injection molding. It gives me a sense of fulfillment and connection to society when I see a car on the road with a product we helped make.
Plant Profile
Name
- Hiroshima Plant
Established
- March 1974
Number of Employees
- 96 (as of FY2024)
Location
708 Takehara, Yoshida-cho, Akitakata-shi, Hiroshima 731-0511, Japan MAP
- TEL+81-826-43-0721
Site Area
- 15,500㎡
Business Area
Acquisition Certification
- ISO9001
- IATF16949
- ISO14001
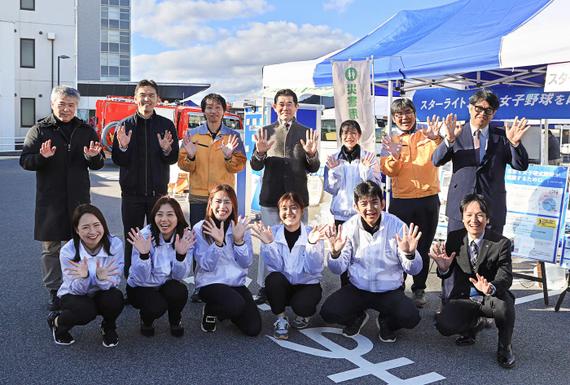
We look forward to working in partnership with you to create new solutions. Leading society to the right direction.
We make proposals to solve social issues with competence products and services while valuing our connection to nature and society. Please feel free to contact us.
Inquiry