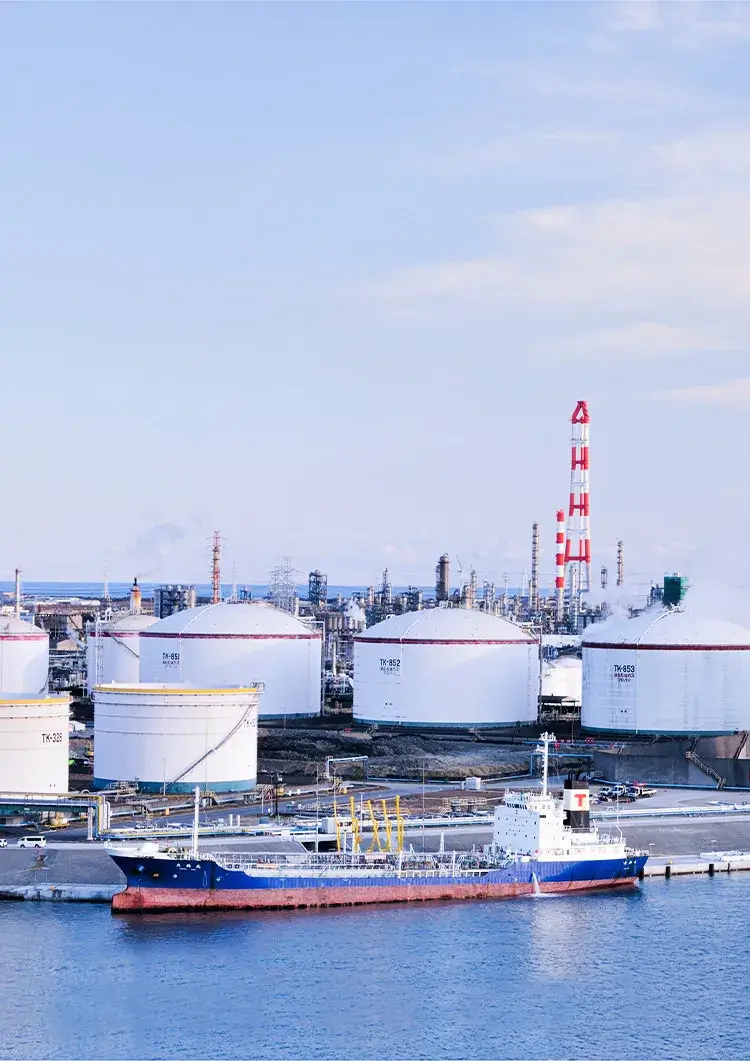
Tribology Business
As a solution provider, we support society's infrastructure
with friction, wear, and lubrication technologies.
Based on tribology technologies embodying the concept of "Slide," "Hold," and "Seal", we are constantly in pursuit of advanced technologies ahead of the market needs and promoting product proposals with our strength in developing unique resin materials according to the required friction performance.
We provide one-stop solutions based on material design, molding and processing, and evaluation and analysis technologies to achieve optimization and labor saving in a variety of applications and production equipment, including industrial machinery, robots, electrical and electronic equipment, and mobility and transportation.
STARLITE'S STRENGTHS
- Utilizes compound technology
that meets friction performance - Demonstrates performance evaluation
and analysis technology for product design - Proposes molding and processing technologies
that optimize costs
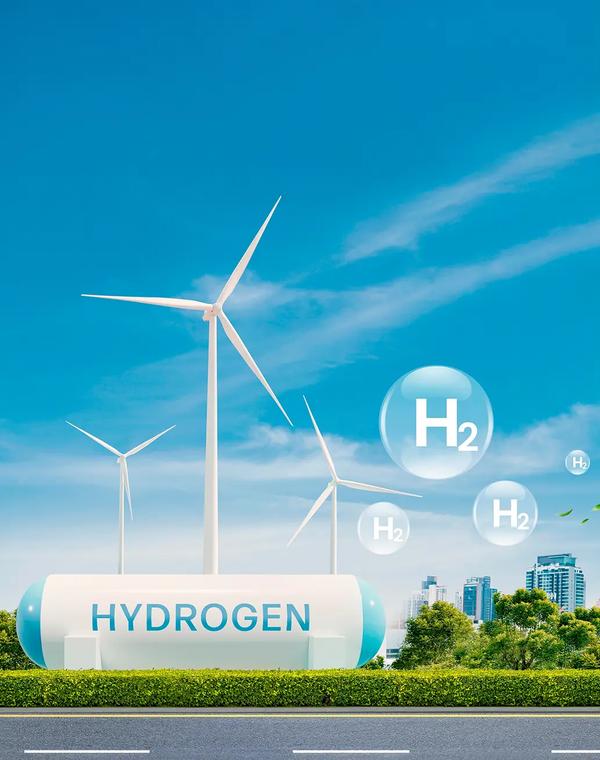
Lead a new energy society with its excellent dynamic sealing characteristics.
Starlite’s ALP® seal rings demonstrate the excellent sealing characteristics in all kinds of gas atmospheres by proposing shapes and specifications that match the operating environment. For example, they have excellent sliding properties even in a high-pressure hydrogen atmosphere and achieve high durability and a long service life. The rings are also used in hydrogen production plants and hydrogen stations, where they ensure stable sealing performance even when storing liquid hydrogen at cryogenic temperatures.
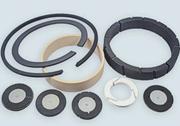

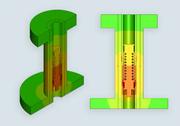
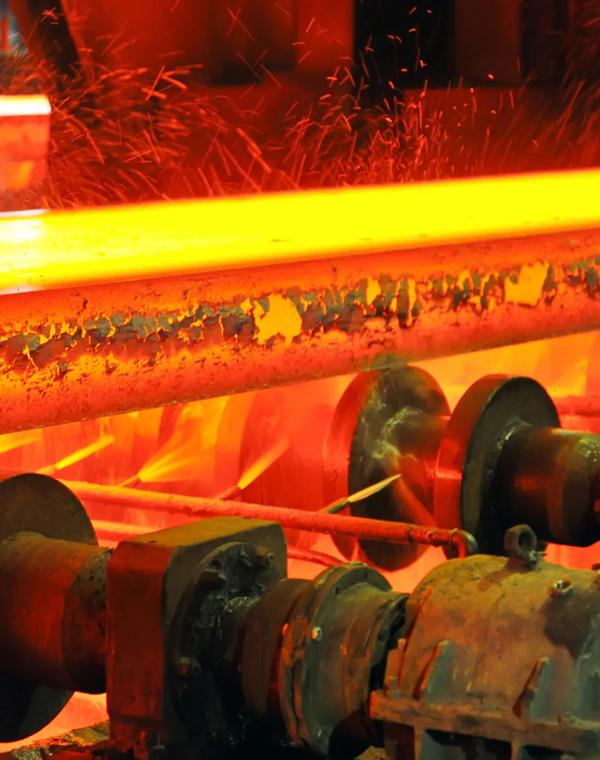
Support the world's key industries with optimal material design that suits the demands of harsh environments.
BAKES®, a thermosetting resin material made primarily from phenolic resin using our own material and molding technologies, has about 80 years of experience in scratch resistant products for steel rolling mills that support Japanese industry and rudder bearings for large ships. We will continue to make proposals to meet the tough demands that are considered difficult to solve with resin and to support society's infrastructure.
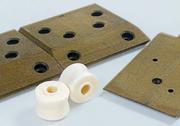
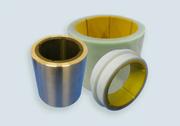
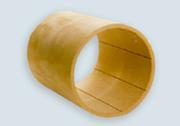
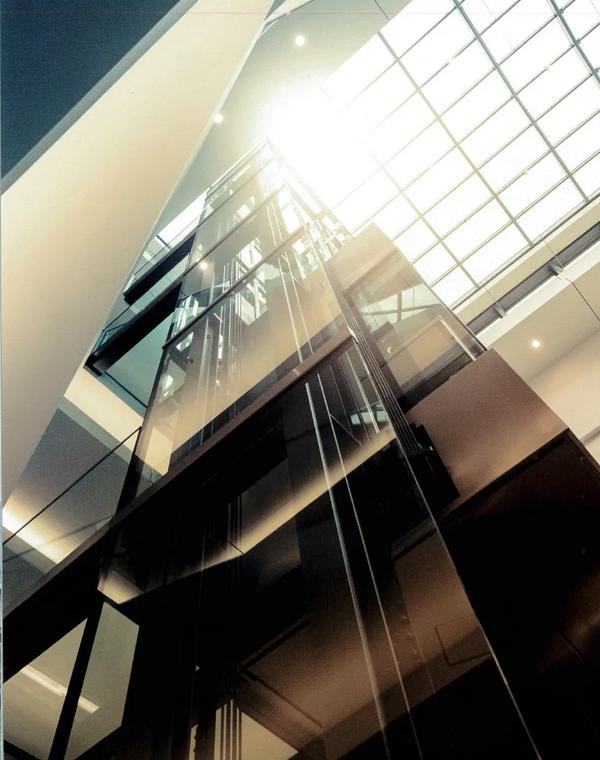
Have excellent durability and heat resistance with optimal friction characteristics and is also eco-friendly.
Starlite’s friction materials are used to "hold" in harsh environments, including preventing elevators from swaying when stopped and smoothing the movement of robot arms. We also promote sustainability through biomass-based products that reduce CO2 emissions, improve performance, and reduce waste through longer service life.
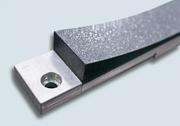
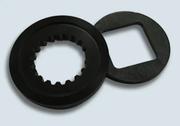
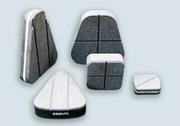
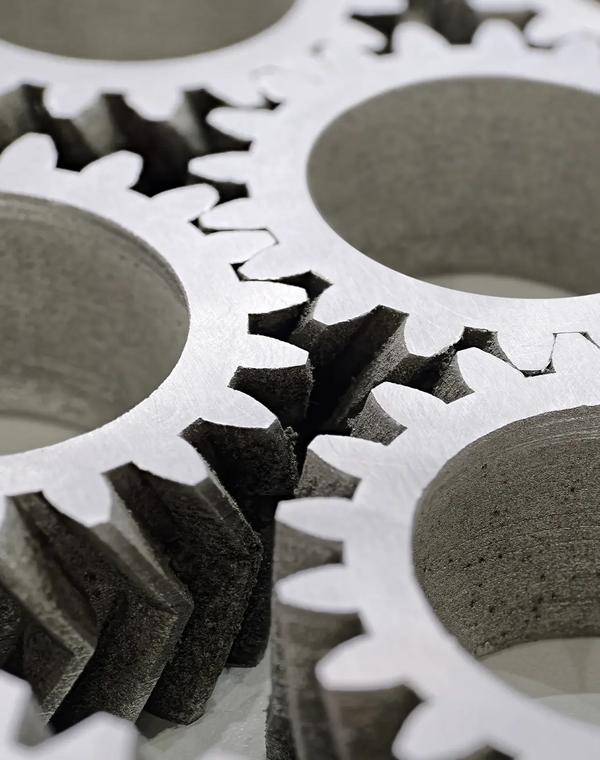
Meet needs with optimal mechanical proposals and verification for motion engineering.
S-BEAR®, a material for injection molding based on super engineering plastics, is used where wear resistance and high durability are required, such as automobiles, robots, and office equipment. Our strengths lie in short-term, high-precision product development using CAE, and we meet needs such as space-saving, grease-free, and low-noise by selecting materials that match the required performance, customizing designs, and performing motion analysis that captures torque variations.
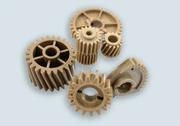
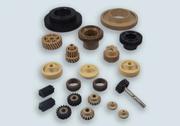
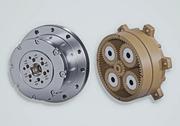
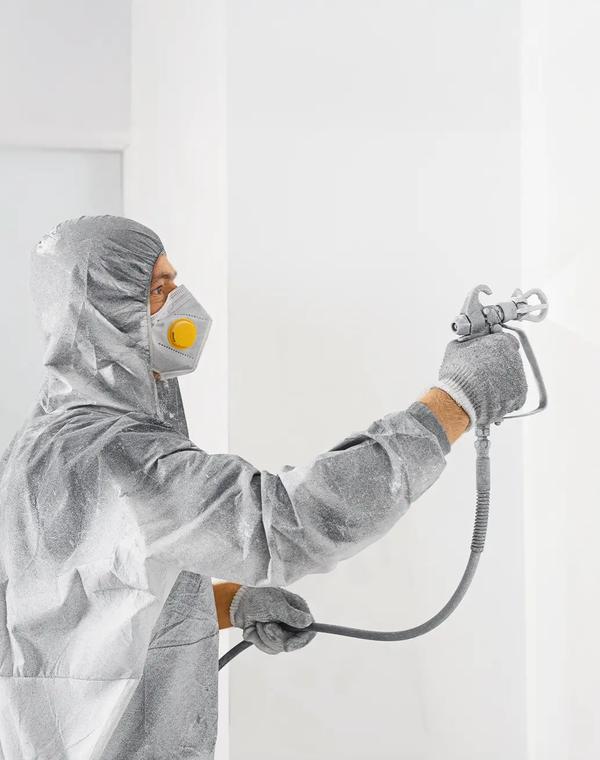
Provides impact resistance, wear resistance, and high durability by applying polyurea coating.
BARIAS® is a coating technology using polyurea resin, which has high impact resistance. For example, the coating is used for marine fenders and playground equipment where impact resistance is required. It also improves safety and maintainability by making lightweight materials, such as foams, stronger, preventing flaking and the spread of cracks in walls and concrete surfaces, and extending the service life of equipment and facilities.
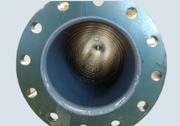
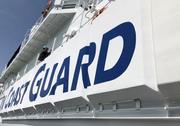
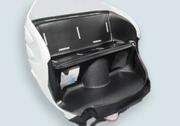
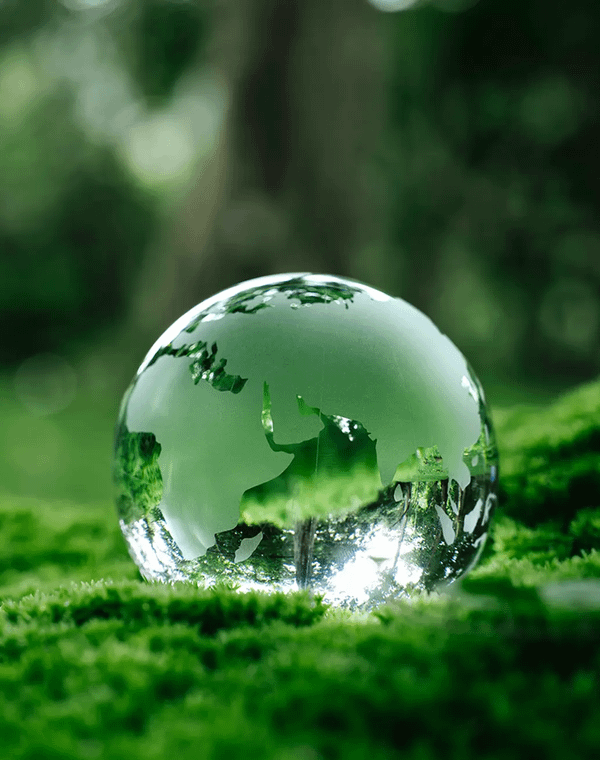
Propose next-generation tribology technology for a sustainable society.
Even for super high-performance products for limited applications, environmental friendliness is essential. Therefore, we are actively taking on the following challenges to achieve a sustainable society.
- Develop materials with better sliding properties than existing petroleum-based products using non-petroleum-derived engineering plastics.
- Propose to reduce waste through not only material development, but recycling of offcuts during
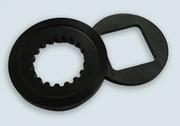
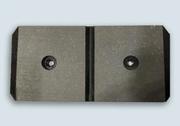
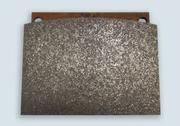
STARLITE turns the customer's demands asking “Step further” into competence.
More specifically, we proposed ways to reduce environmental burden and work efficiency, including energy saving, oil-free, long life, control of friction characteristics, compact and light gear units, reinforcement of severely deteriorated parts, and reduction of removal work by stick prevention.